I started "gunsmithing" with a 7x10 mini lathe, moved to a 10x24 Atlas, and about 2 weeks ago I acquired and placed an 11x37" Rockwell lathe in my shop. Now that I have a lathe that has a quick change gearbox and a 1.4" spindle bore I have started to do some barrel work. My first thing to do was play with an old 10/22 barrel that Im sure most of us have laying around. I cut the barrel to 16.25", moved the front sight base back, threaded 1/2x28, and made a nice knurled thread protector outta the spare barrel piece.
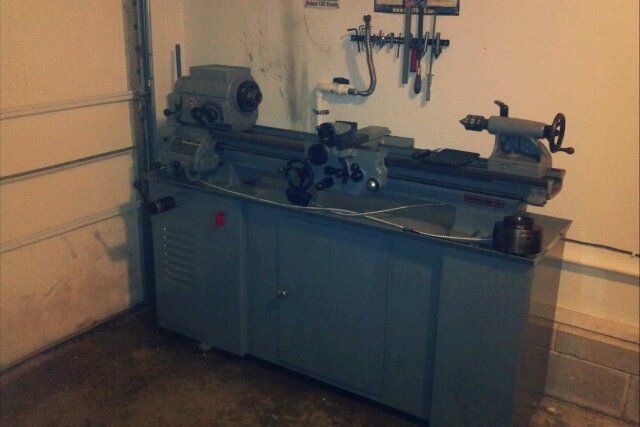
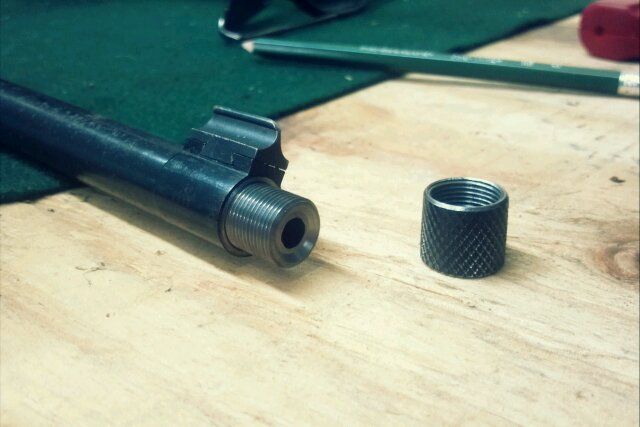
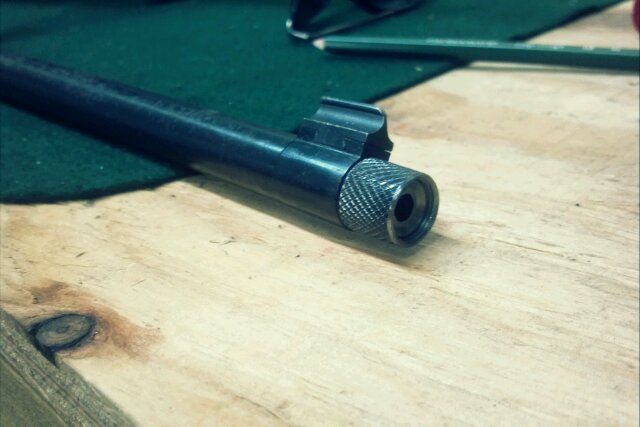