I got one of Viper's action truing fixtures as I've heard they are nice for doing short barrels on my long (18 inches or so--22 with the chuck) spindle (https://shop.pacifictoolandgauge.com/index.php?main_page=product_info&cPath=5_28&products_id=1457) and it is a nice solid fixture, but I'm getting chatter while cutting both tenon and threads. I believe it is all that unsupported length hanging off in space. I had to slow down to about 175 rpm to do the cuts and it took forever. I usually do threading at 175, but I had to drop to 64 rpm and still got chatter. Any clues?
Should I try a live center in the bore? I dial in the bore to within a tenth or so, but I know my tailstock is about 2 tenths off in the z-plane.
Setup for tenon work (Click for hi-res):
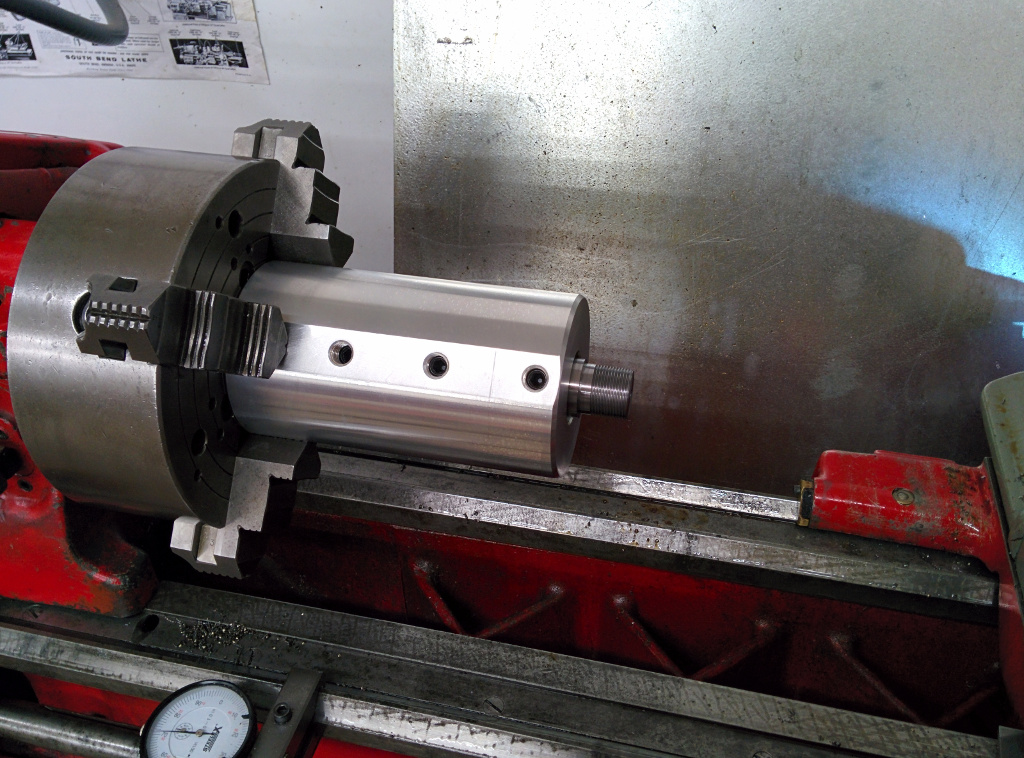
Notice chatter on the threads and also where I tried to cut some relief at the shoulder (click for hi-res):
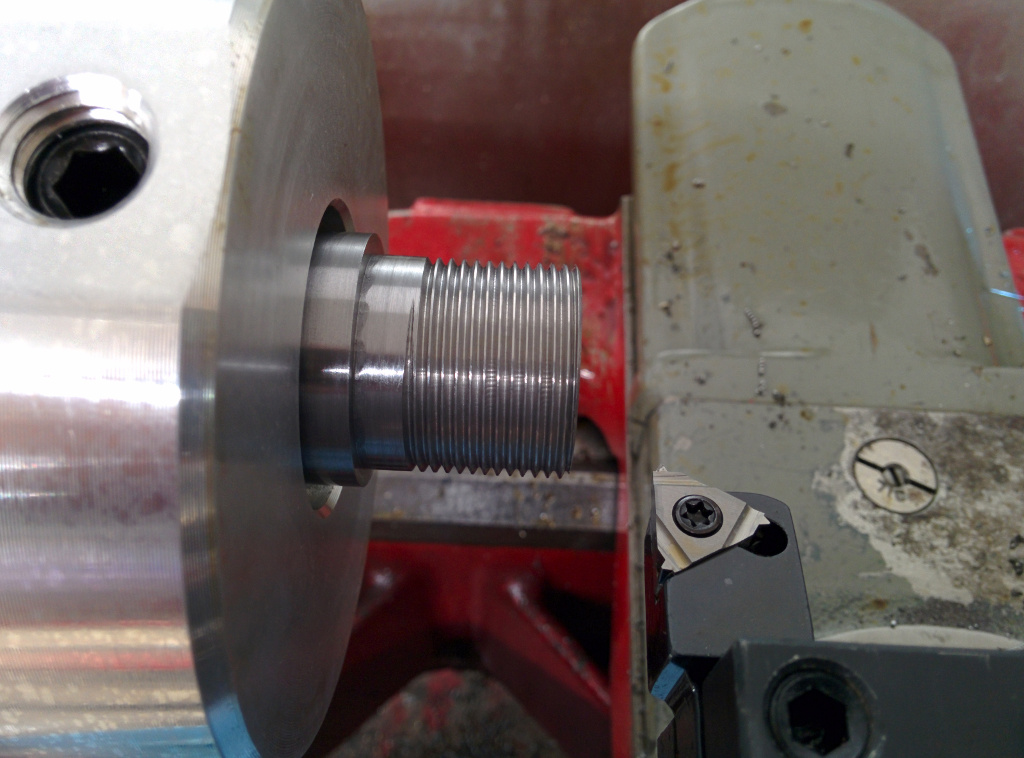
The action fits great:
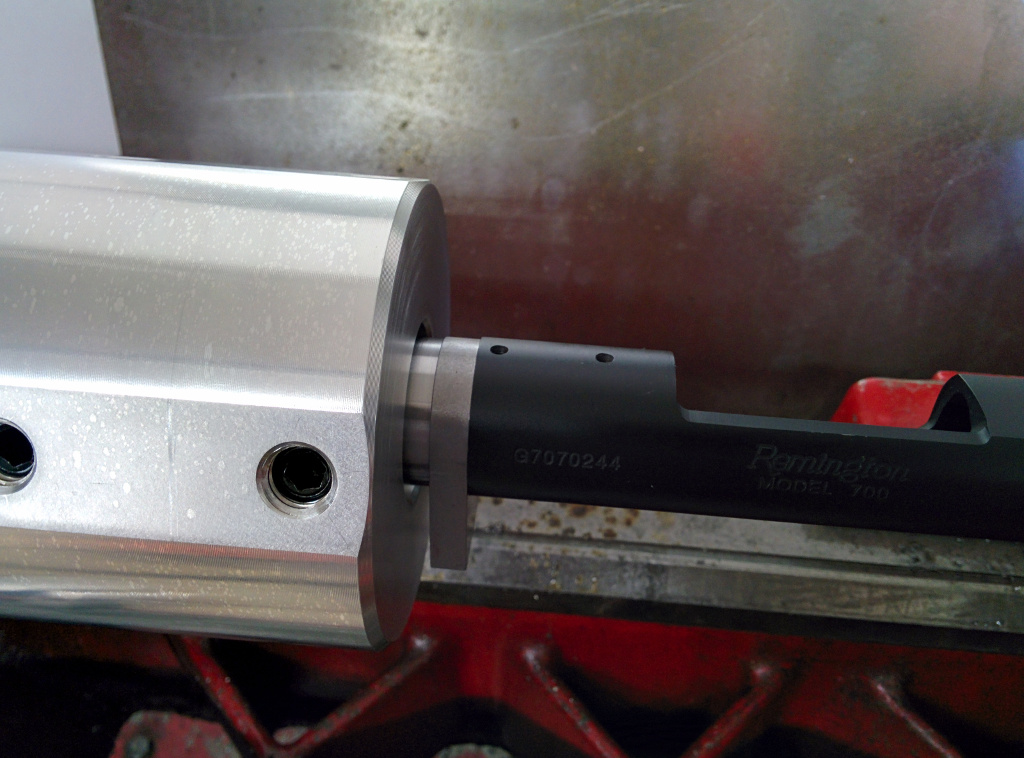
Should I try a live center in the bore? I dial in the bore to within a tenth or so, but I know my tailstock is about 2 tenths off in the z-plane.
Setup for tenon work (Click for hi-res):
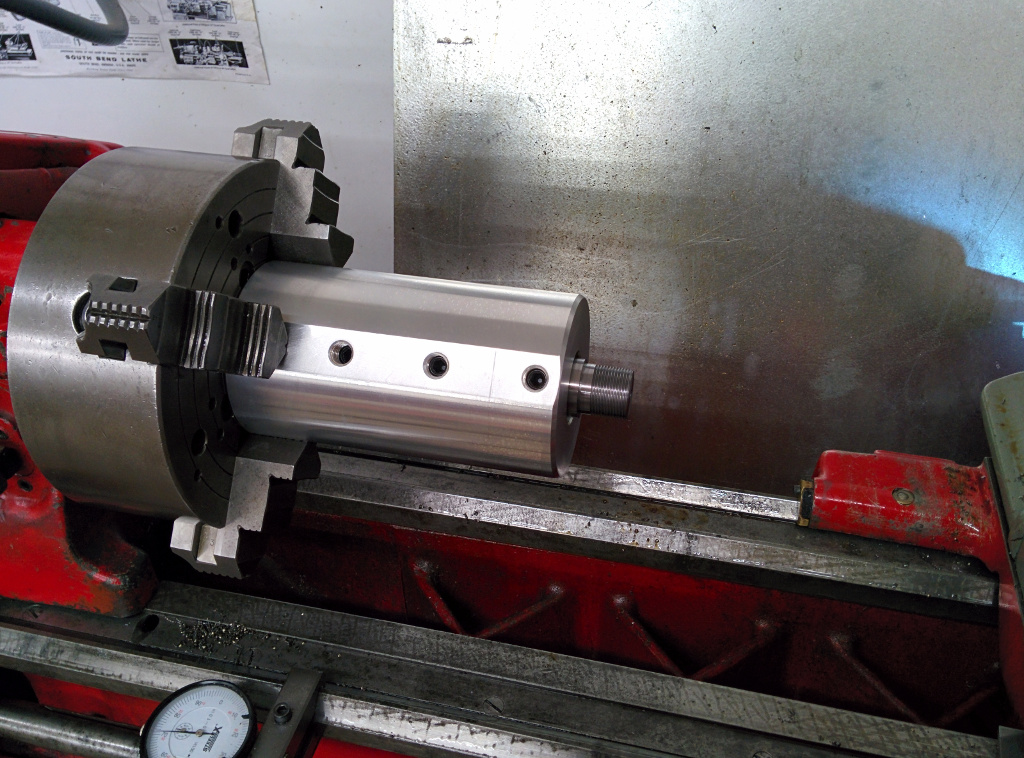
Notice chatter on the threads and also where I tried to cut some relief at the shoulder (click for hi-res):
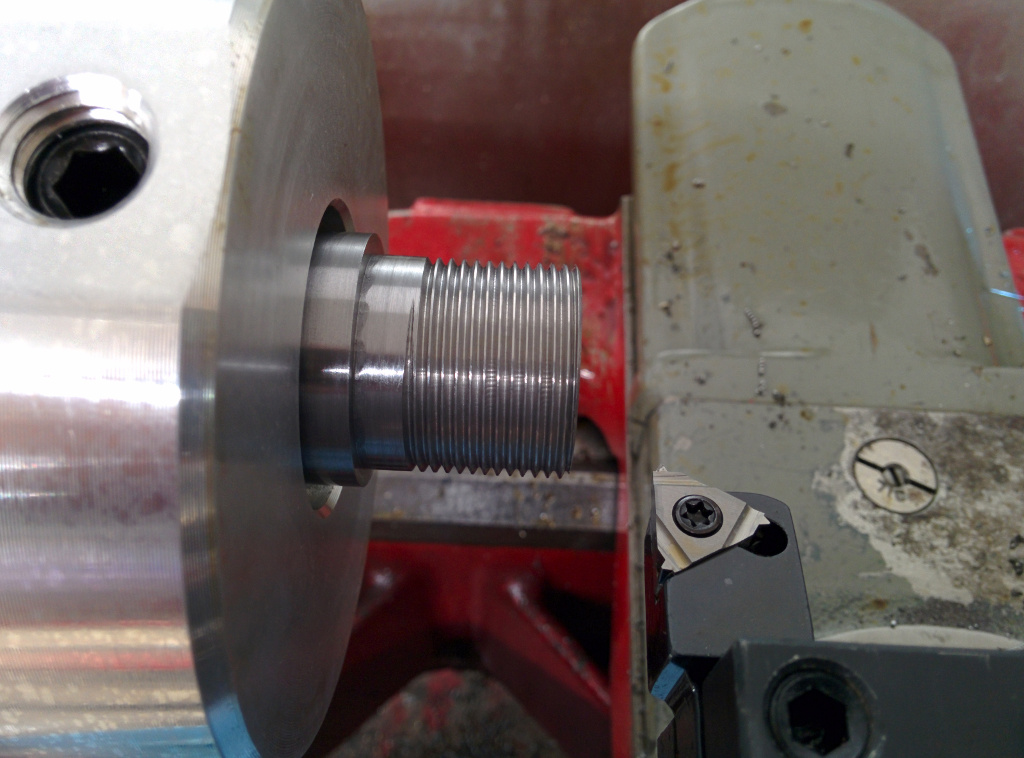
The action fits great:
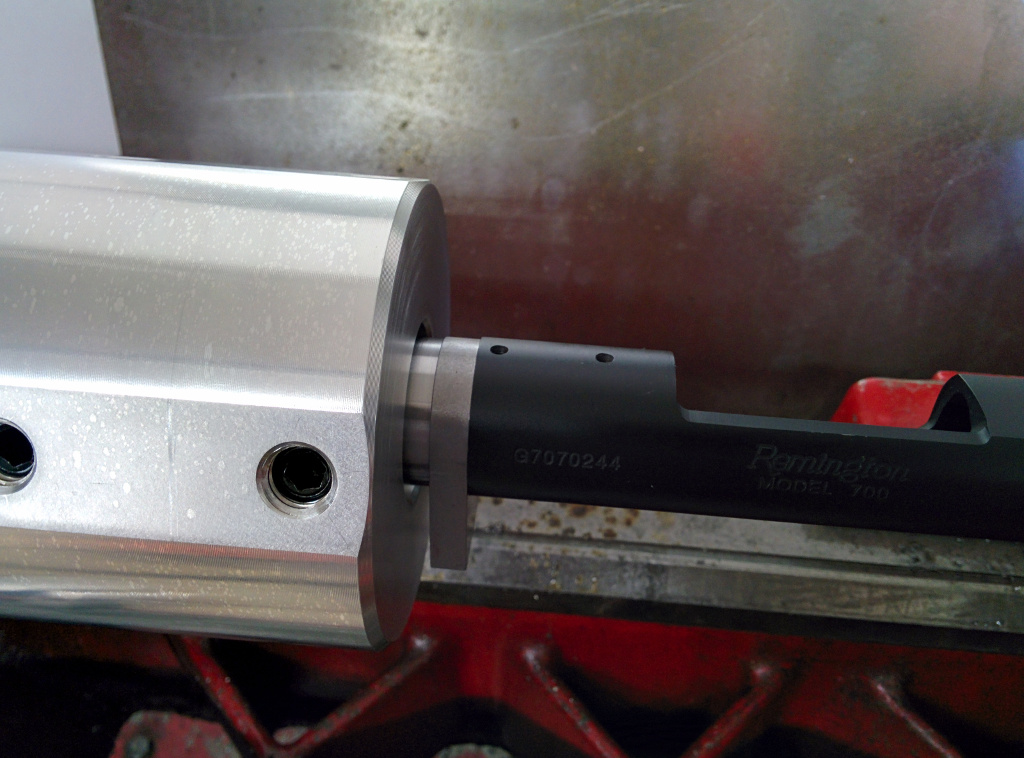