Well over the weekend I decided to build my front spider for my 11" Rockwell lathe. I built a rear spider about 2 months ago and have been using the Set-Tru feature of my Buck chuck to indicate barrels for threading. While this works it is not quick, precise, or ideal. Having not purchased a 4-Jaw yet (working on that), I dug through my scrap bin and found a drop off piece of 5" diameter bar of some unknown metal and pulled out a spare L00 buck backplate I bought and went too work. I wish now I would have taken pictures of the process but alas, I did not. Now the hardest part of this endevour for me was drilling and tapping the adjustment screw holes. I only have a Harbor Freight Micro-Milling machine so i dont have nearly enough room to drill them on the mill. So time to get creative. I ended up attaching the material to the cross slide and drilling the holes on the lathe. It worked but wasnt prefect. After I got that hurdle jumped, I drilled the mounting holes in the face of the spider and the backplate to match and bolted it all together. Still waiting on my 1/2x20tpi screws for the adjustments but you get the idea. I can now work an 18" barrel in the headstock.
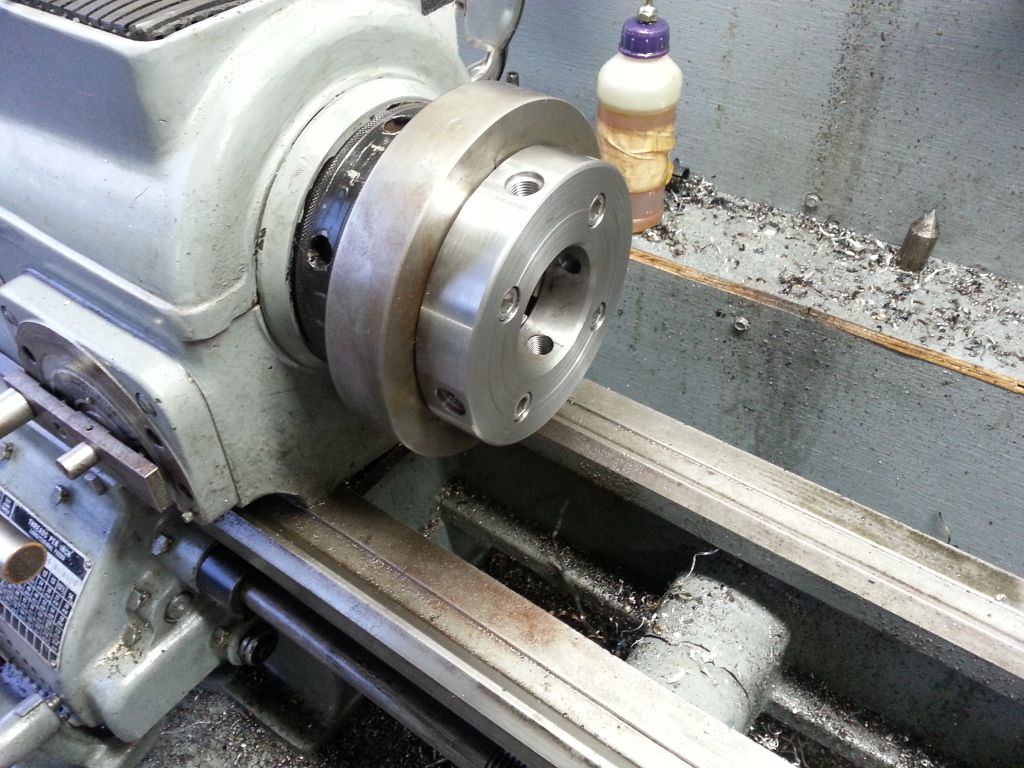
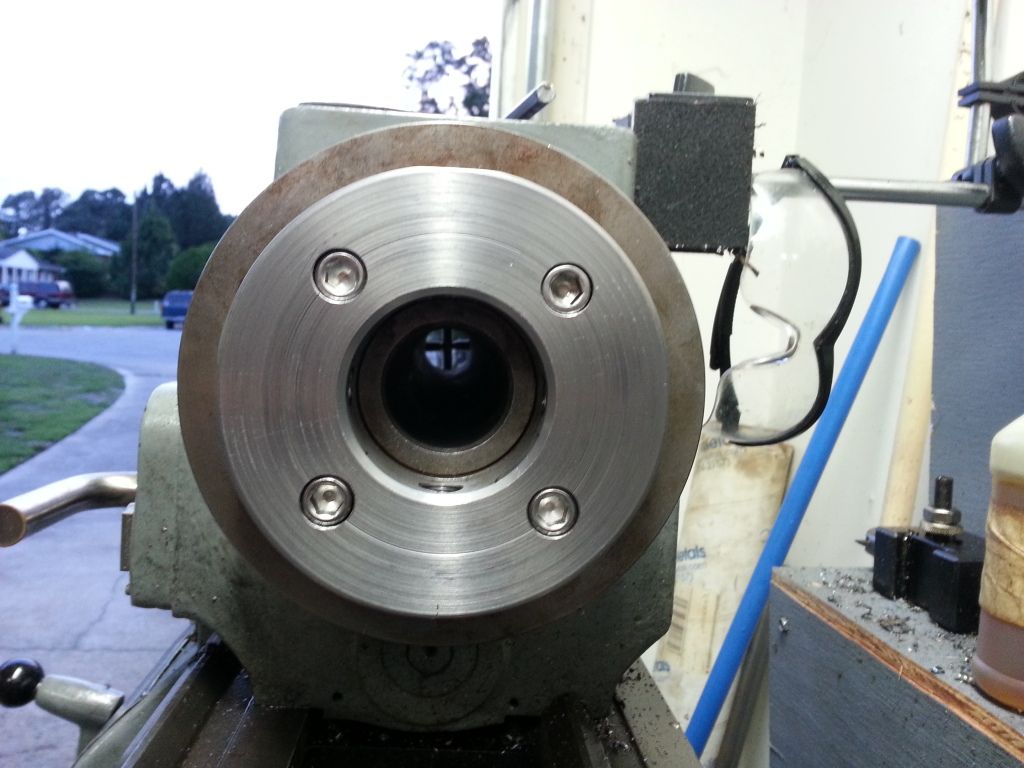
The rear spider threads onto the rear of the spindle and uses 3/8x24tpi adjustment bolts.
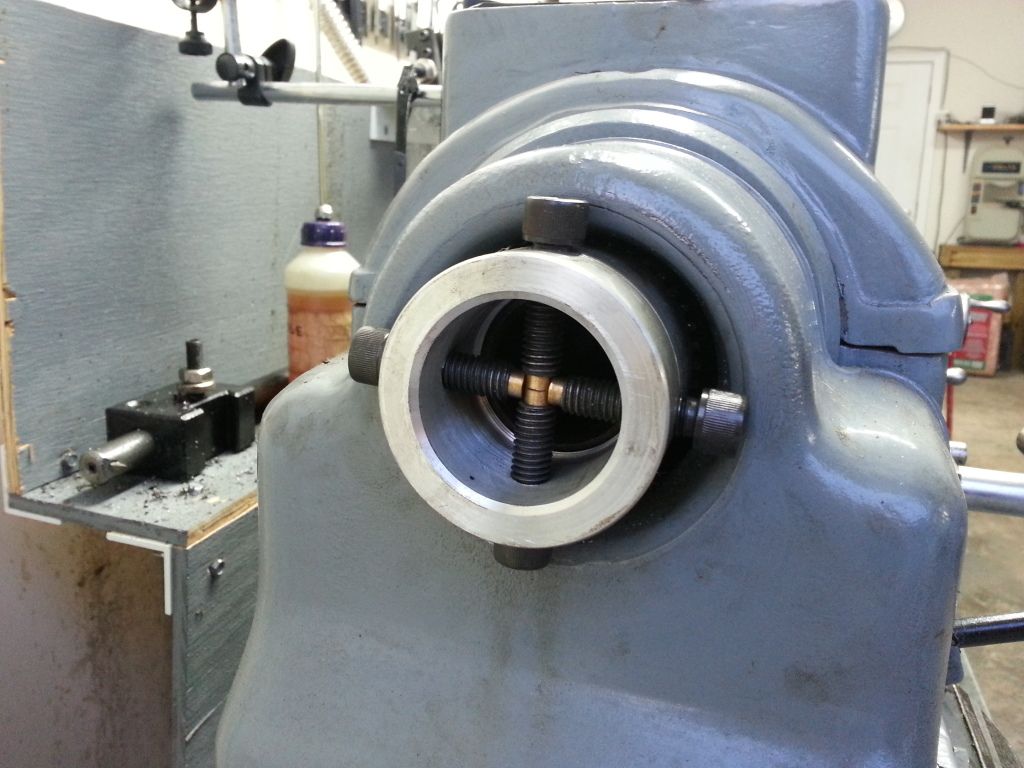
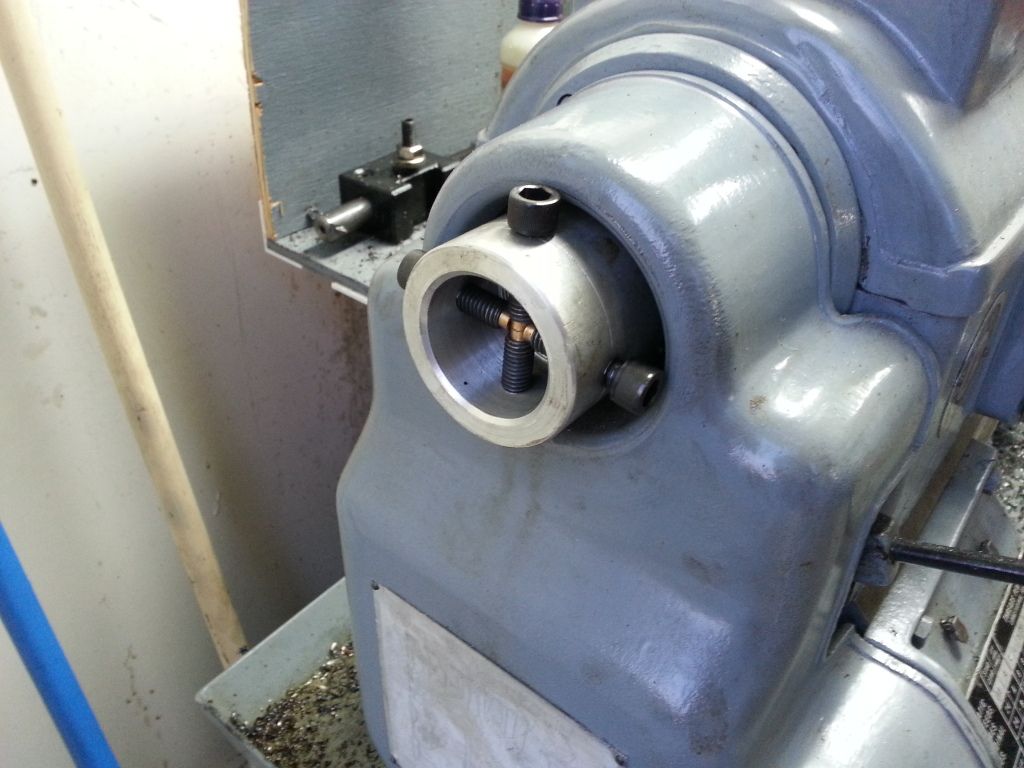
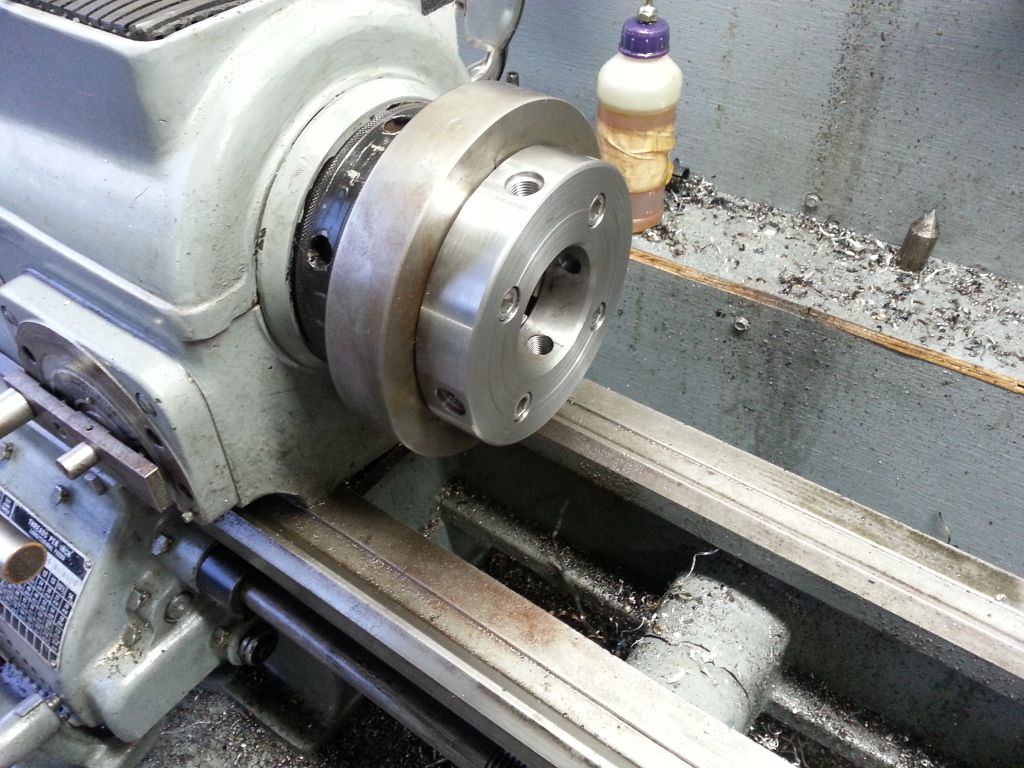
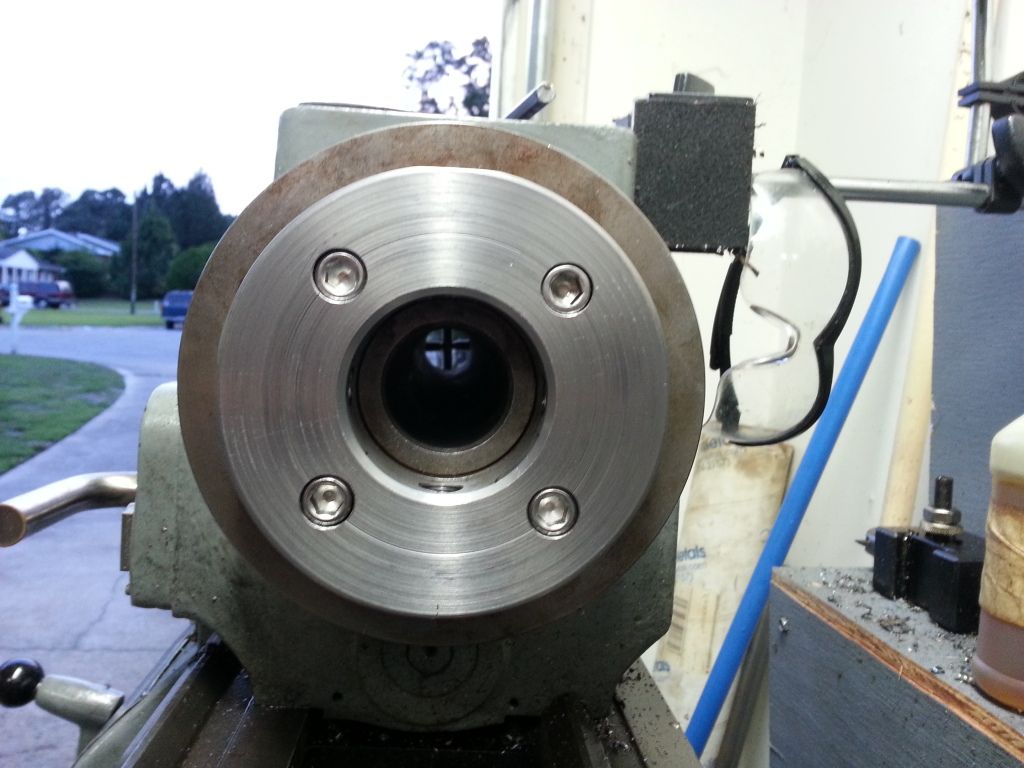
The rear spider threads onto the rear of the spindle and uses 3/8x24tpi adjustment bolts.
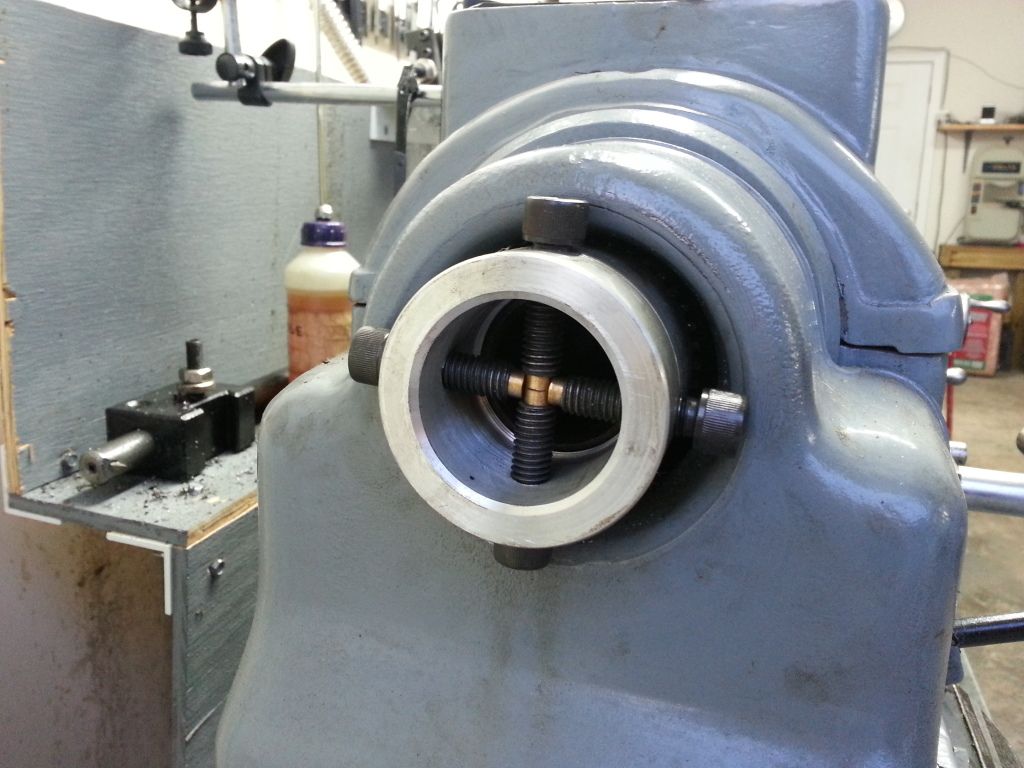
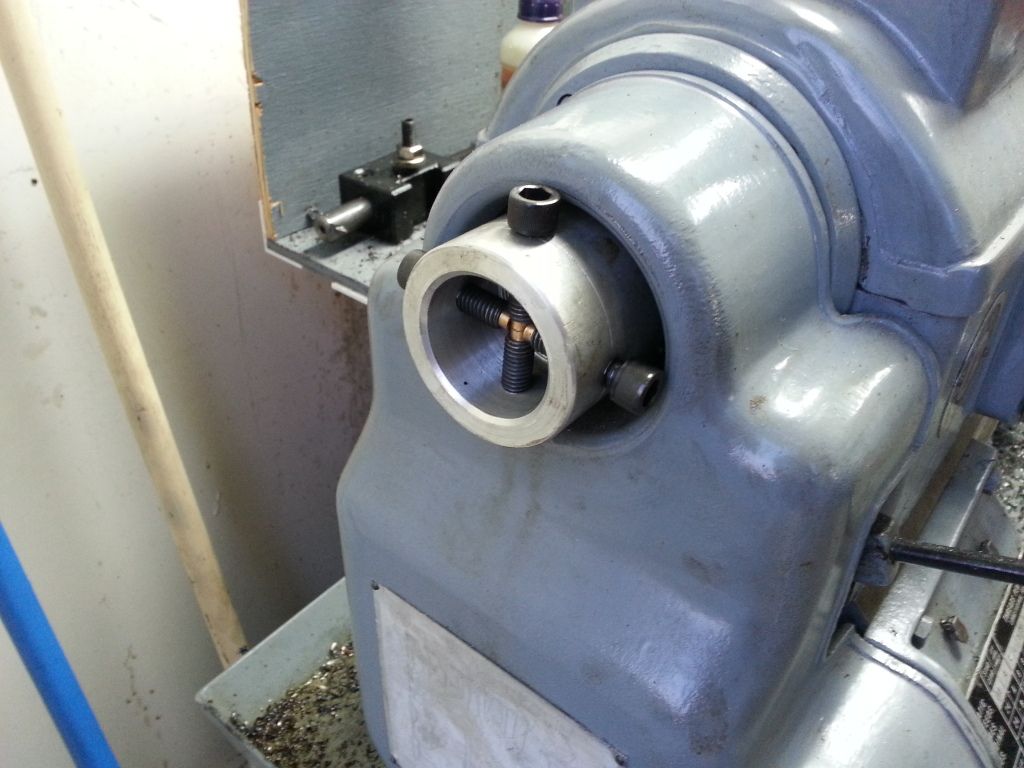