I recently sold my good 'ol Benchsource annealing machine to "upgrade" to the latest induction technology and bought an AMP after reading numerous positive reviews on it. I love the concept and the simplicity and consistency that this is supposed to bring to this process but my experience so far is less than great.
The first machine I received was clearly defective since the LED read-out kept distorting every 10-15 seconds. Brownell's was great and quickly replaced it. The second one seems to be functioning as intended, I guess. I figured I would start out practicing on some of my piles of once-fired Hornady 6.5 Creedmoor brass before giving it a go with the much more expensive Lapua stuff I mainly shoot now.
The first challenge I encountered was the varied settings on their website that are lot specific. Of course, none of my lots were listed. I realize that the company offers free analysis of your brass but the catch is fairly pricey shipping to New Zealand for every lot that's not already there, and I have many. This is not a knock on the company or their customer service which I believe are rock solid.
To be safe, I used the lowest setting found for the majority of the Hornady lots listed. The problem as you see below is that at least 10% of the brass I annealed crushed like grapes upon resizing. I even slightly backed off the bump on my Forster Micrometer resizing die since their instructions recommend that due to the fact that annealed brass won't "bounce back" like non-annealed brass will tend to do. I've never had any issues with these dies in the past.
I'm curious if others have run into this kind of problem and/or have any suggestions? If I can't figure it out, I might just return it and go back to my old fashioned torch method where I never crushed a single cartridge.
thx.
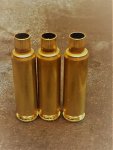
The first machine I received was clearly defective since the LED read-out kept distorting every 10-15 seconds. Brownell's was great and quickly replaced it. The second one seems to be functioning as intended, I guess. I figured I would start out practicing on some of my piles of once-fired Hornady 6.5 Creedmoor brass before giving it a go with the much more expensive Lapua stuff I mainly shoot now.
The first challenge I encountered was the varied settings on their website that are lot specific. Of course, none of my lots were listed. I realize that the company offers free analysis of your brass but the catch is fairly pricey shipping to New Zealand for every lot that's not already there, and I have many. This is not a knock on the company or their customer service which I believe are rock solid.
To be safe, I used the lowest setting found for the majority of the Hornady lots listed. The problem as you see below is that at least 10% of the brass I annealed crushed like grapes upon resizing. I even slightly backed off the bump on my Forster Micrometer resizing die since their instructions recommend that due to the fact that annealed brass won't "bounce back" like non-annealed brass will tend to do. I've never had any issues with these dies in the past.
I'm curious if others have run into this kind of problem and/or have any suggestions? If I can't figure it out, I might just return it and go back to my old fashioned torch method where I never crushed a single cartridge.
thx.
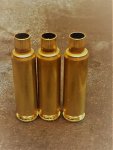
Last edited: