We typically don't get much demand for jeweled bolts, but a gent asked for it and I'd not done it in a long time so I figured what the hell... But, I didn't have any tooling for it. Watched a couple vids on U toob and decided to try something a little different.
So here's what I did. Works pretty cool.
Get a 1/4" od brass rod and cut it around 3" long. (so that you have enough standoff to avoid hitting the handle on the bolt) Face one end clean in the lathe.
Using a small boring bar face the brass rod clean and finish by cutting a shallow "crown" on the end of the piece. Just a shallow angle so that the face is "dished" by a few degrees. All I did was run the machine in reverse and use the draft angle of the boring tool to create the angle.
Now shut off the machine. Lock the carriage so that you can only move in the X axis (cross slide) Set your tool so that it scribes a line across the face of the dish you just cut. Basically were going to use the lathe as a shaper tool. Just needs to be a few .001's deep. Make a pass, worked best for me from the backside towards center. Now rotate the chuck a small amount and repeat till you get a sort of knurled face on the brass rod. This serves as a tooth for the jeweling pad to attach to. That comes next.
Cut two postage stamp size pieces of leather and super glue them together. I get better luck having the rough side of the leather exposed on both ends.
Leaving your brass stick in the chuck, throw your drill chuck in the tail stock and run the jaws to fully closed. Now position it about an inch from the face of your part and lock the tailstock down to the bed.
Place your leather pad next to the brass rod and spot a dab of superglue on the rod. Using your free hand, run the chuck into the leather and squish it against the brass rod. Let is set a minute or two to fully setup.
So here's what I did. Works pretty cool.
Get a 1/4" od brass rod and cut it around 3" long. (so that you have enough standoff to avoid hitting the handle on the bolt) Face one end clean in the lathe.
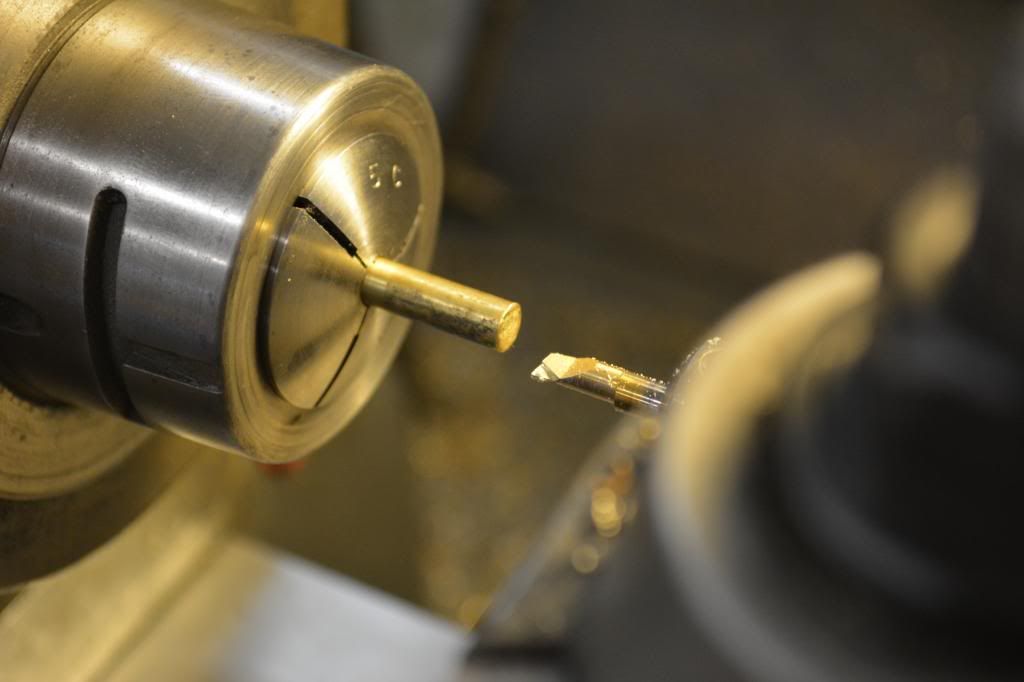
Using a small boring bar face the brass rod clean and finish by cutting a shallow "crown" on the end of the piece. Just a shallow angle so that the face is "dished" by a few degrees. All I did was run the machine in reverse and use the draft angle of the boring tool to create the angle.
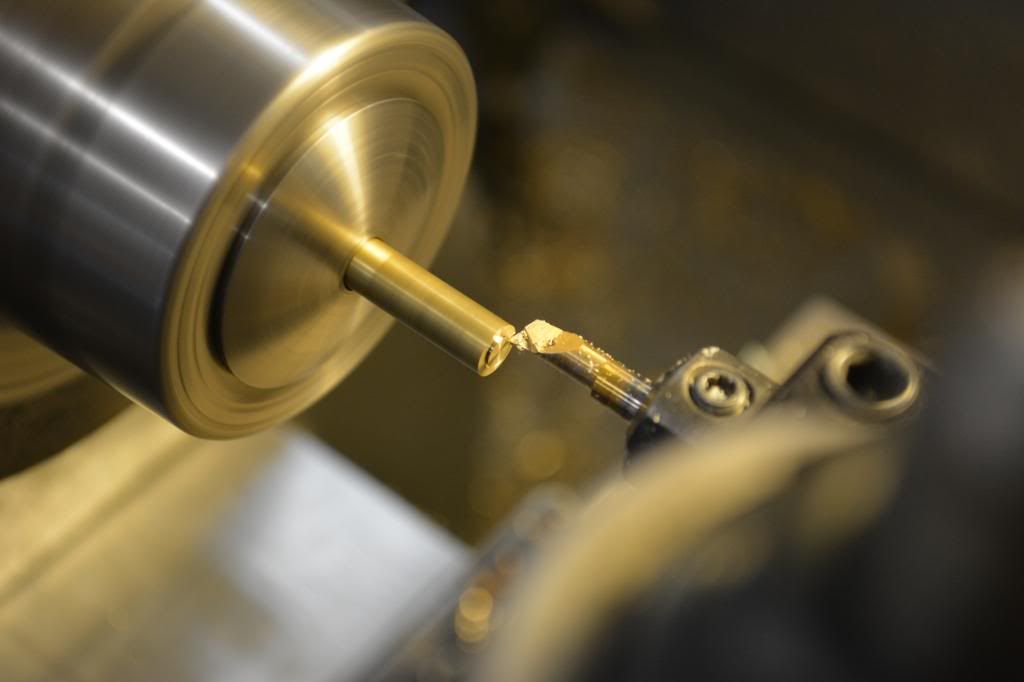
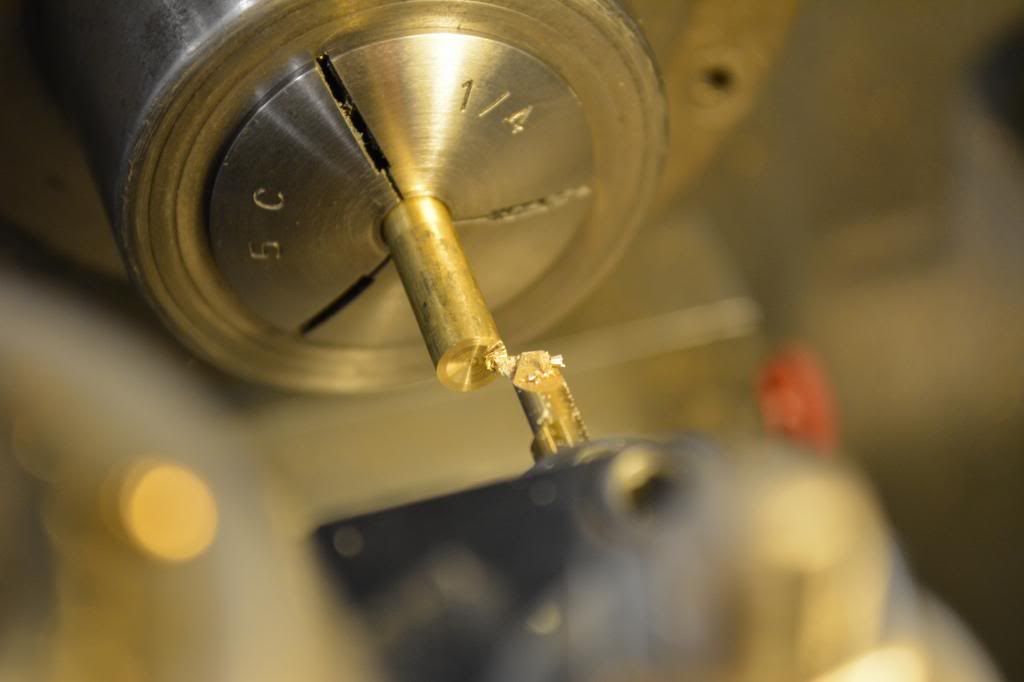
Now shut off the machine. Lock the carriage so that you can only move in the X axis (cross slide) Set your tool so that it scribes a line across the face of the dish you just cut. Basically were going to use the lathe as a shaper tool. Just needs to be a few .001's deep. Make a pass, worked best for me from the backside towards center. Now rotate the chuck a small amount and repeat till you get a sort of knurled face on the brass rod. This serves as a tooth for the jeweling pad to attach to. That comes next.
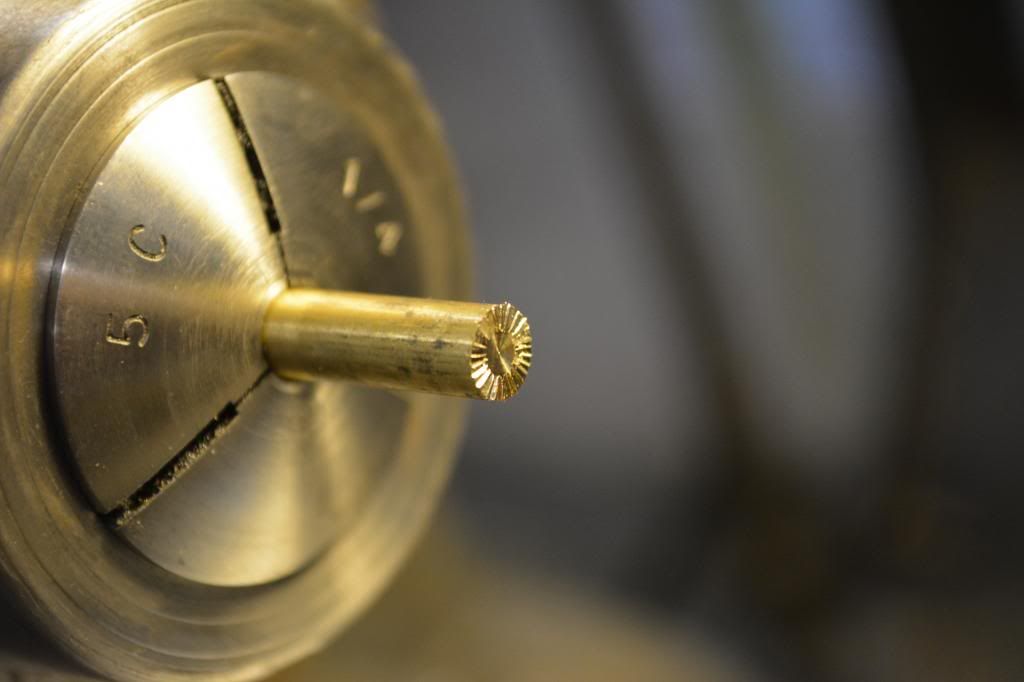
Cut two postage stamp size pieces of leather and super glue them together. I get better luck having the rough side of the leather exposed on both ends.
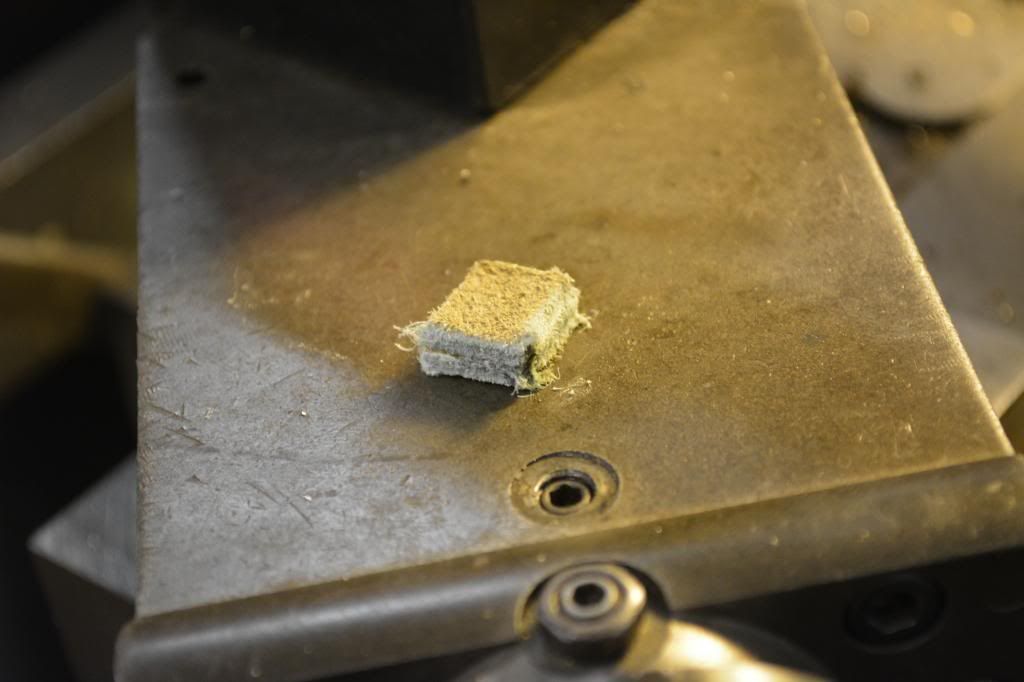
Leaving your brass stick in the chuck, throw your drill chuck in the tail stock and run the jaws to fully closed. Now position it about an inch from the face of your part and lock the tailstock down to the bed.
Place your leather pad next to the brass rod and spot a dab of superglue on the rod. Using your free hand, run the chuck into the leather and squish it against the brass rod. Let is set a minute or two to fully setup.
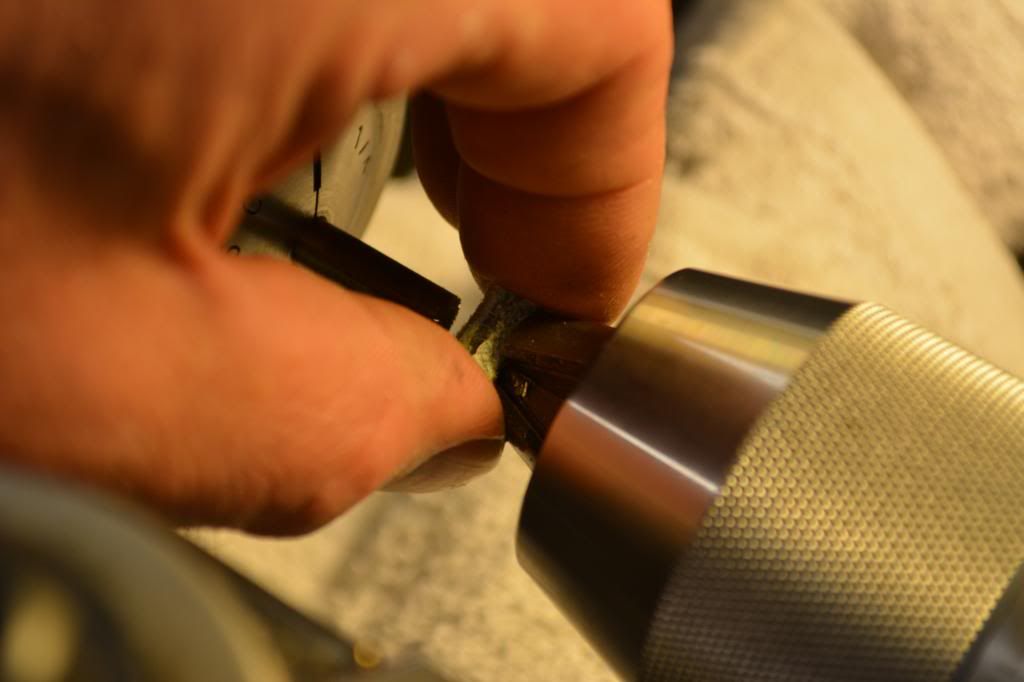
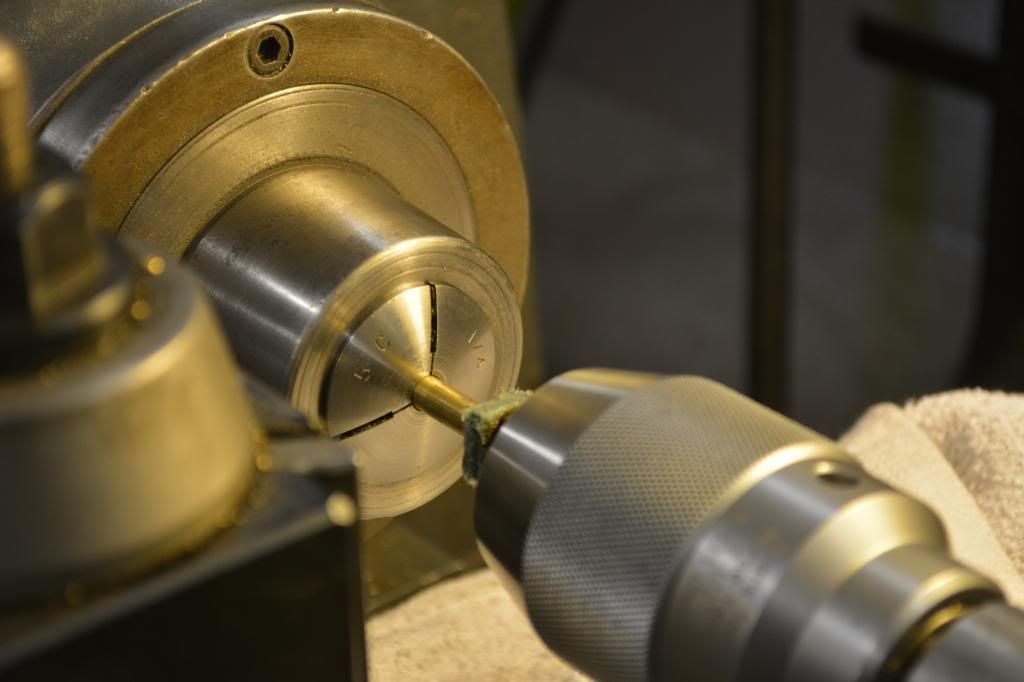
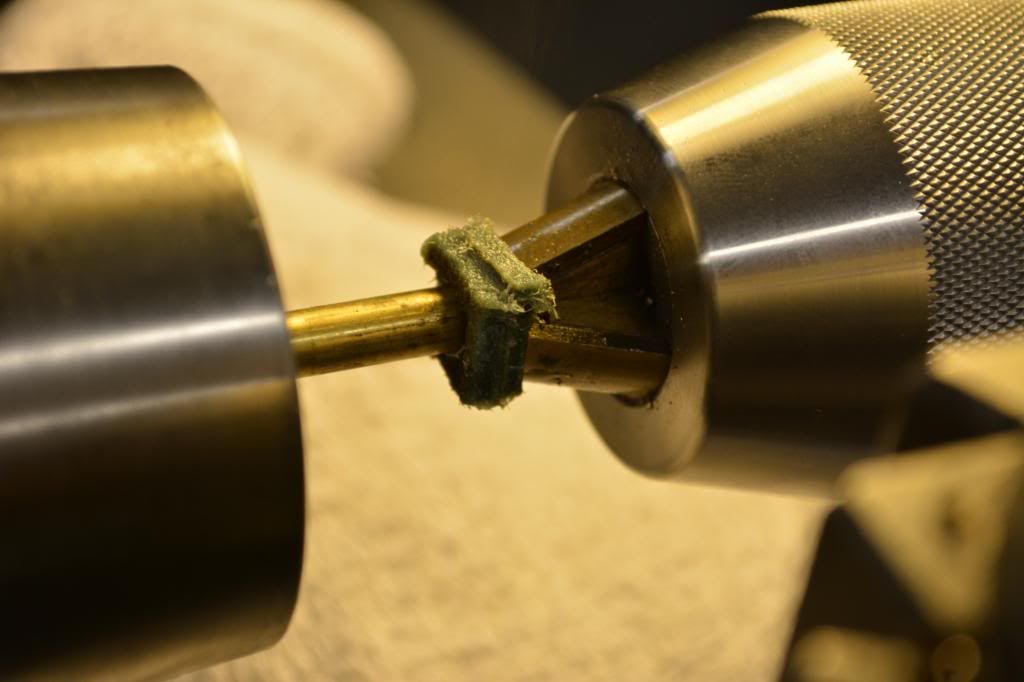