Disclaimer ... I am new to reloading!!!
I just finished full length resizing a 40 round batch of 7mm rem mag brass..
now my question is should my headspace reading on each individual piece of brass not be the same?
I worked the first piece of brass by slowly increasing the depth on the die until I went from the fired case measurements of around 2.115-2.117 headspace
down to 2.112 which was my .003 goal...
now set the die locked it down and measured the next piece and 2.111 so I was happy with that and proceeded to resize the rest of the batch.
Now my question still is it normal for the same die on the same set of brass that was locked down the entire batch to have this much of a swing in result? I have 2.108-2.114 here and one stubborn piece that reads 2.116 and I tried to resize it several times... whats the deal????? is this normal is it all good to go? did I do something wrong?
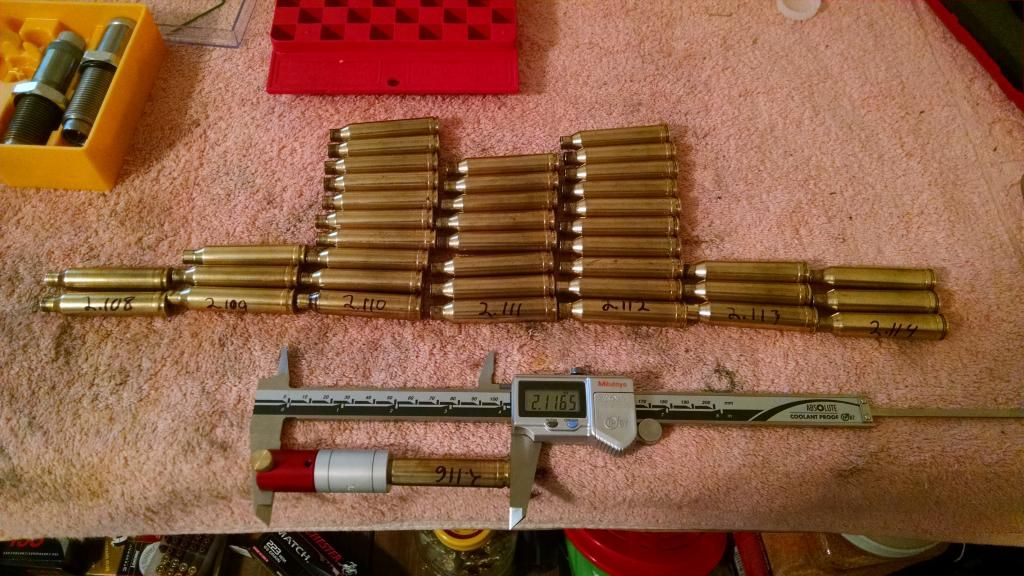
I just finished full length resizing a 40 round batch of 7mm rem mag brass..
now my question is should my headspace reading on each individual piece of brass not be the same?
I worked the first piece of brass by slowly increasing the depth on the die until I went from the fired case measurements of around 2.115-2.117 headspace
down to 2.112 which was my .003 goal...
now set the die locked it down and measured the next piece and 2.111 so I was happy with that and proceeded to resize the rest of the batch.
Now my question still is it normal for the same die on the same set of brass that was locked down the entire batch to have this much of a swing in result? I have 2.108-2.114 here and one stubborn piece that reads 2.116 and I tried to resize it several times... whats the deal????? is this normal is it all good to go? did I do something wrong?
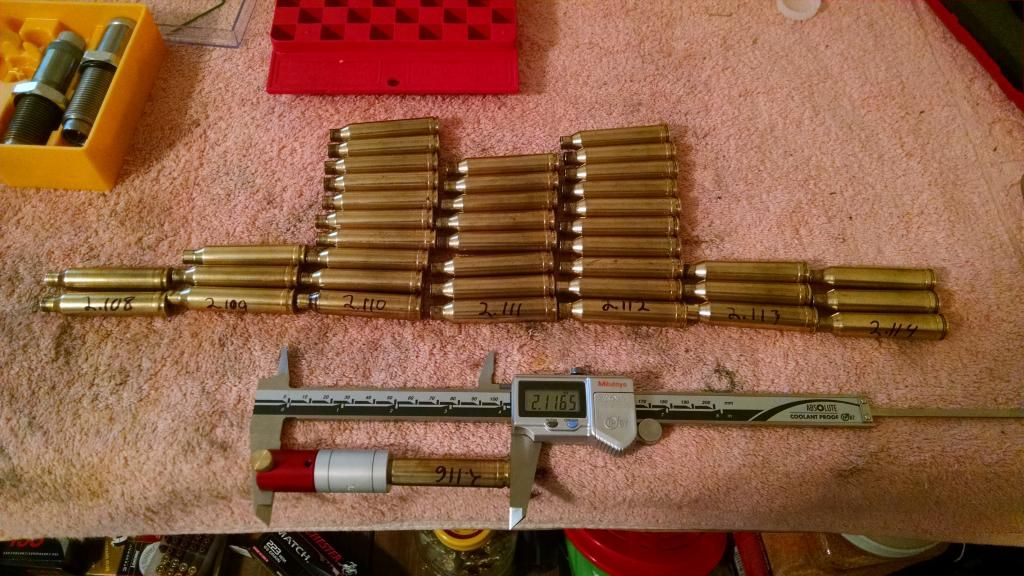