Guys... I am reading a lot of complaining and talk of how simple the work is but I haven't heard any of you talk about the tools and equipment needed to perform the work. Lathe, Mill, reamers, tooling, barrel vise, action wrenches, gauges, punches, bench grinders, belt sanders, hand tools and not to mention the specialty tools required for certain jobs. All of this comes at a huge price. It's a craftsman trade for sure. Yes anyone can do most of the stuff with practice and training. However, I don't see many of you taking on the task. Alibi: I am not referring to slapping an AR together.... that isn't armorer work.
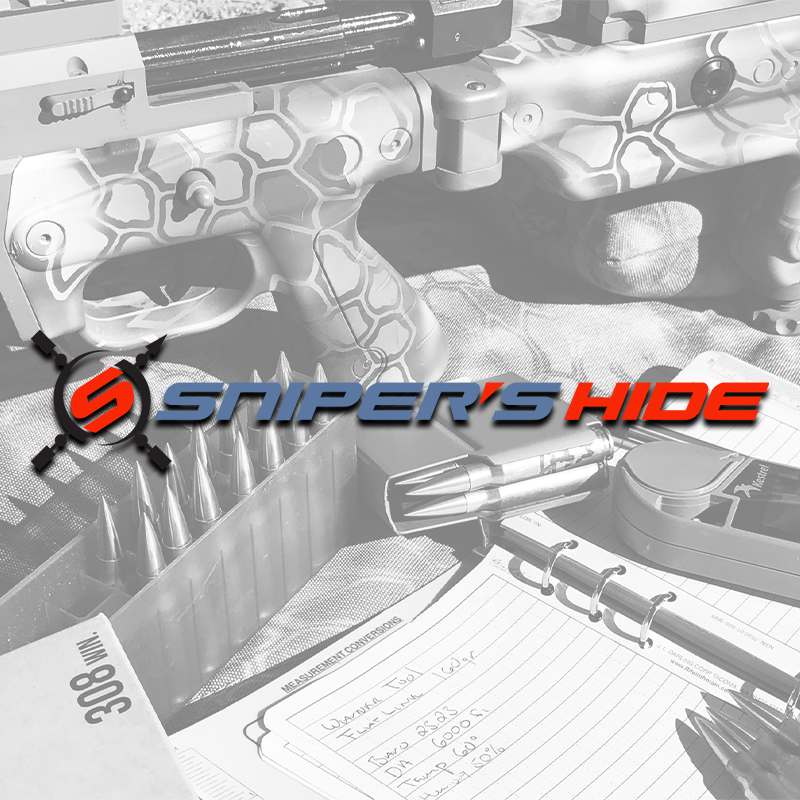
Gunsmith etiquette
When, if ever, is the right time to check in on the progress of a build? Dropped one off in February and there was a 16 week lead time on the barrel. REM 700 action to get trued as well as threading and chambering. I’m not rushing, I’m just curious. My first foray into this.