We do a PILE of these. It's probably the single most popular upgrade on an existing rifle stock. Fortunately, the procedure is pretty straight forward and one we've become very comfortable with.
Goes like this.
Step one: Qualify the holes in the stock where the screws go. I ream these to 5/16" as my alignment pins are this size. The pins register the stock in the fixture to get it close. Stocks can vary a bit so its rarely a drop in and go type setup. I have to orient the computer program to the position of the stock in the fixture. Easy enough to do.
Here's a coaxial indicator showing position on the two holes. We seat the rear to zero for X/Y and move to the front. S/A M700 type receivers are generally around 6.5" center to center on the spacing. So we rapid over to that distance and check the front. In this case it was 6.503" in X and -.004" in Y. Pretty close, but we'll adjust the program to get it spot on.
Goes like this.
Step one: Qualify the holes in the stock where the screws go. I ream these to 5/16" as my alignment pins are this size. The pins register the stock in the fixture to get it close. Stocks can vary a bit so its rarely a drop in and go type setup. I have to orient the computer program to the position of the stock in the fixture. Easy enough to do.
Here's a coaxial indicator showing position on the two holes. We seat the rear to zero for X/Y and move to the front. S/A M700 type receivers are generally around 6.5" center to center on the spacing. So we rapid over to that distance and check the front. In this case it was 6.503" in X and -.004" in Y. Pretty close, but we'll adjust the program to get it spot on.
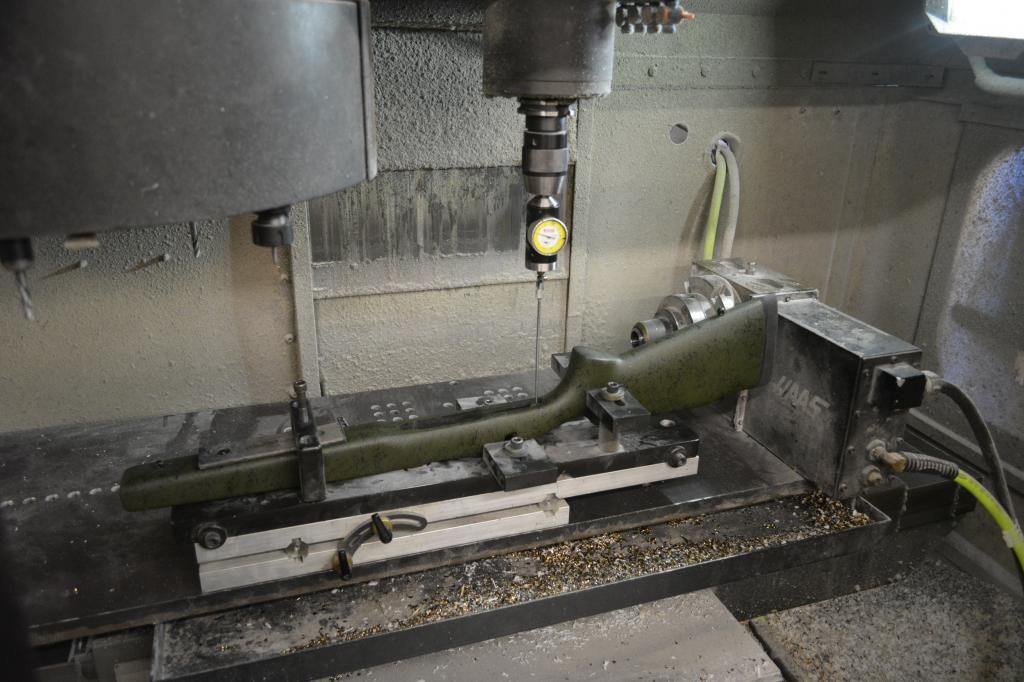
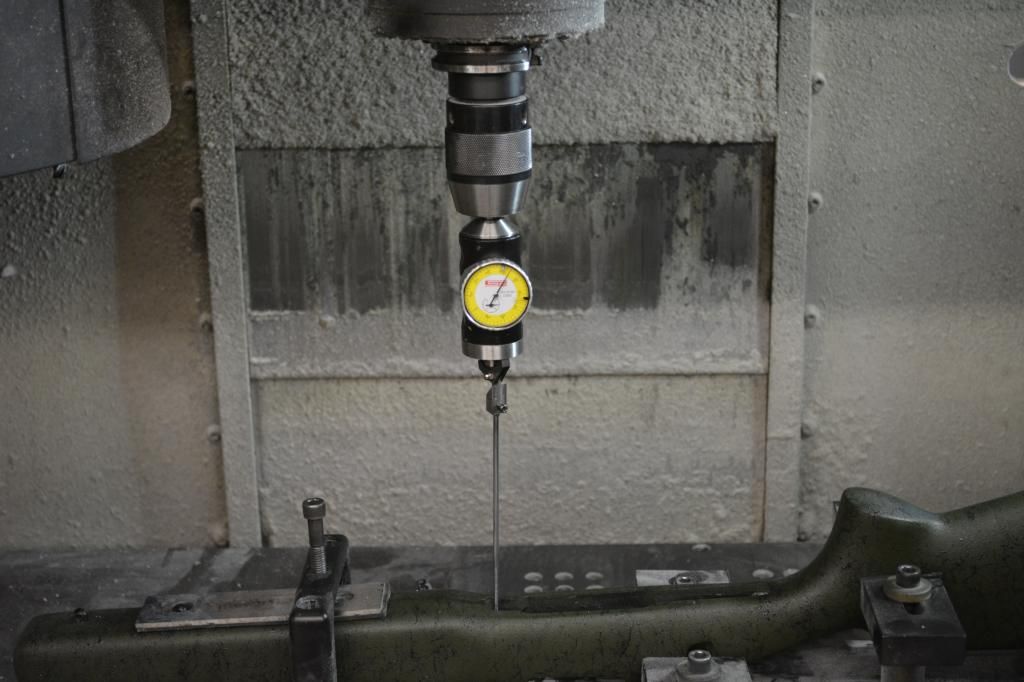
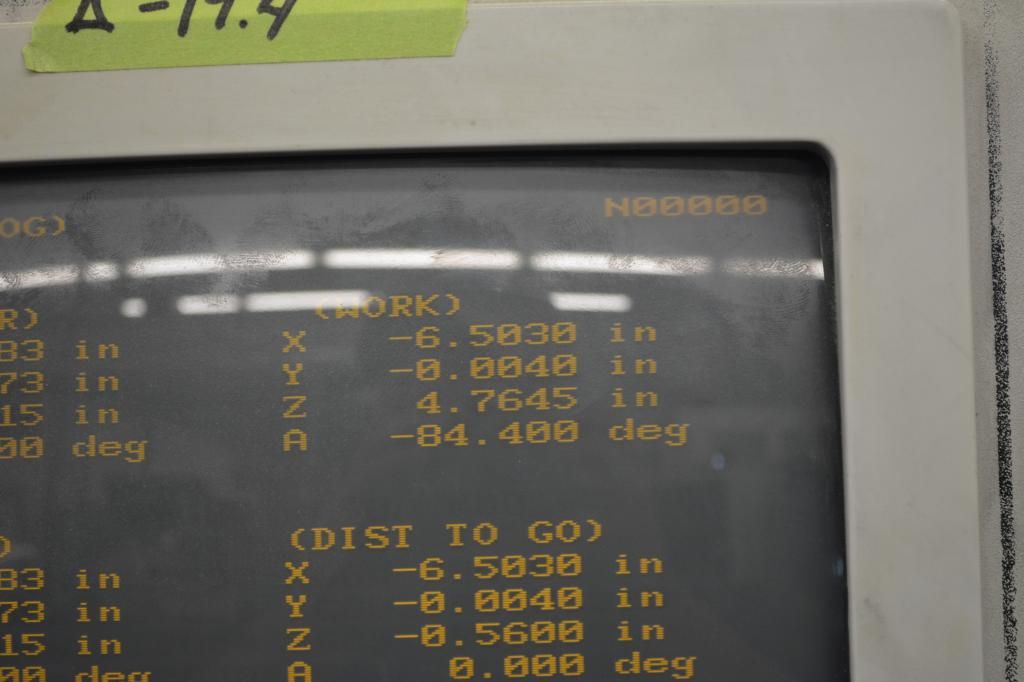