Ok,
Without naming names, I sent my Lilja barrel for my CZ 455 to a well regarded smith here on the hide to be threaded for my Sparrow. When I received it back, my Sparrow would not thread all the way to the shoulder. I did a bit of research and it turns out he made a common mistake- he threaded it to AR-15 spec 1/2x28, which leaves the threads about .500" long, where most .22 suppressors call for .400". I felt a bit like he should have known better, I did tell him that I would be threading on a Sparrow, but hey, mistakes happen, right?
So I sent the barrel back to him, this time including the specs that Silencerco supplies on their site. Plug it all into the CNC machine, and nothing could go wrong, right? Well, not exactly. I get it back, and now the thread protector I paid $40 for no longer evenly mates the barrel. This would suggest to me that either it or the barrel are not threaded concentric, but I thread my can on, and it by looking down the barrel, concentricity is good. However, the suppressor STILL doesn't thread all the way to the shoulder.
I borrowed a tap to clean up the suppressor threads, didn't help, upon close examination I can see that the threads are actually "closed" on the muzzle, where the threads meet the relief cut. Something about the way the machine cut the threads caused a thread impingement that does not allow the suppressor to thread past the threads into the relief. It can be seen with the eye, though difficult to photograph. I confirmed by reversing my thread protector and threading it on, it also gets hung up.
So $250 later, I still don't have a functionally threaded barrel. I don't really want to send it back to the smith, twice seems enough, and based on the shit fit of the thread protector, I am not overly confident in the machine work of this smith. Hell, I'm relatively pissed I have this much tied up into a thread job that still isn't done right when plenty of places advertise thread jobs for $70, but being pissed won't fix it.
Can I clean the threads up with a die? I believe I need a "class 3" die. Could someone link me one? Or do I need to send it out a third time?
Thanks,
-Bob
Edited to add a photo. You can see where the relief cut meets the threads and the threads to not continue into the relief.
Without naming names, I sent my Lilja barrel for my CZ 455 to a well regarded smith here on the hide to be threaded for my Sparrow. When I received it back, my Sparrow would not thread all the way to the shoulder. I did a bit of research and it turns out he made a common mistake- he threaded it to AR-15 spec 1/2x28, which leaves the threads about .500" long, where most .22 suppressors call for .400". I felt a bit like he should have known better, I did tell him that I would be threading on a Sparrow, but hey, mistakes happen, right?
So I sent the barrel back to him, this time including the specs that Silencerco supplies on their site. Plug it all into the CNC machine, and nothing could go wrong, right? Well, not exactly. I get it back, and now the thread protector I paid $40 for no longer evenly mates the barrel. This would suggest to me that either it or the barrel are not threaded concentric, but I thread my can on, and it by looking down the barrel, concentricity is good. However, the suppressor STILL doesn't thread all the way to the shoulder.
I borrowed a tap to clean up the suppressor threads, didn't help, upon close examination I can see that the threads are actually "closed" on the muzzle, where the threads meet the relief cut. Something about the way the machine cut the threads caused a thread impingement that does not allow the suppressor to thread past the threads into the relief. It can be seen with the eye, though difficult to photograph. I confirmed by reversing my thread protector and threading it on, it also gets hung up.
So $250 later, I still don't have a functionally threaded barrel. I don't really want to send it back to the smith, twice seems enough, and based on the shit fit of the thread protector, I am not overly confident in the machine work of this smith. Hell, I'm relatively pissed I have this much tied up into a thread job that still isn't done right when plenty of places advertise thread jobs for $70, but being pissed won't fix it.
Can I clean the threads up with a die? I believe I need a "class 3" die. Could someone link me one? Or do I need to send it out a third time?
Thanks,
-Bob
Edited to add a photo. You can see where the relief cut meets the threads and the threads to not continue into the relief.
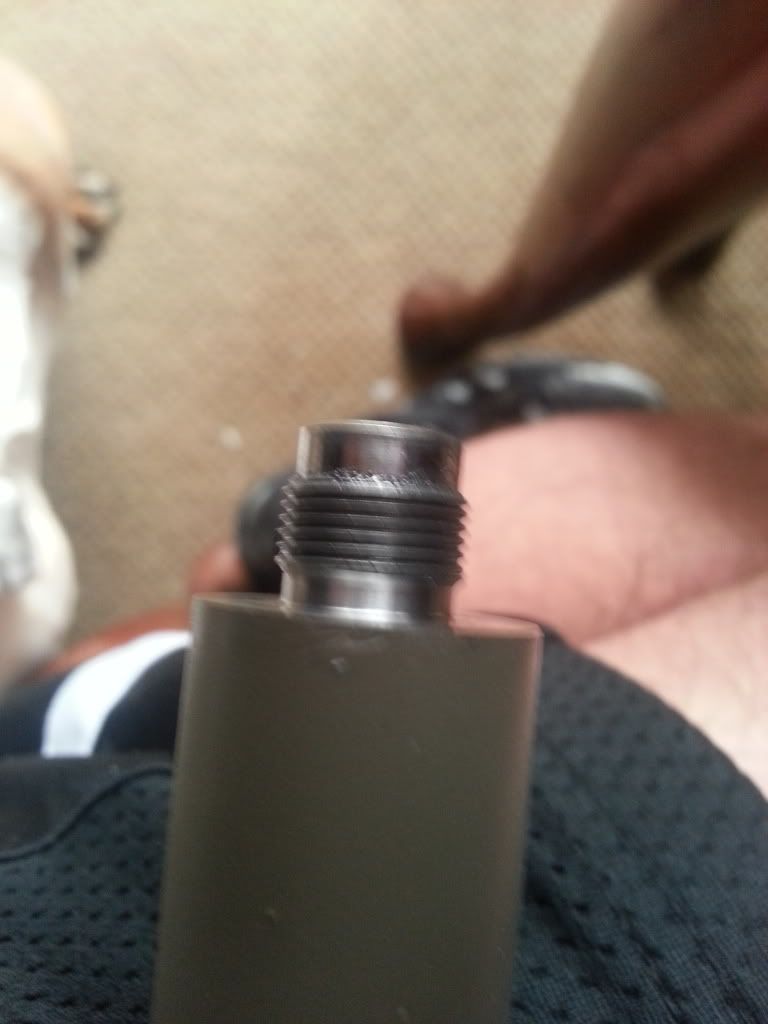
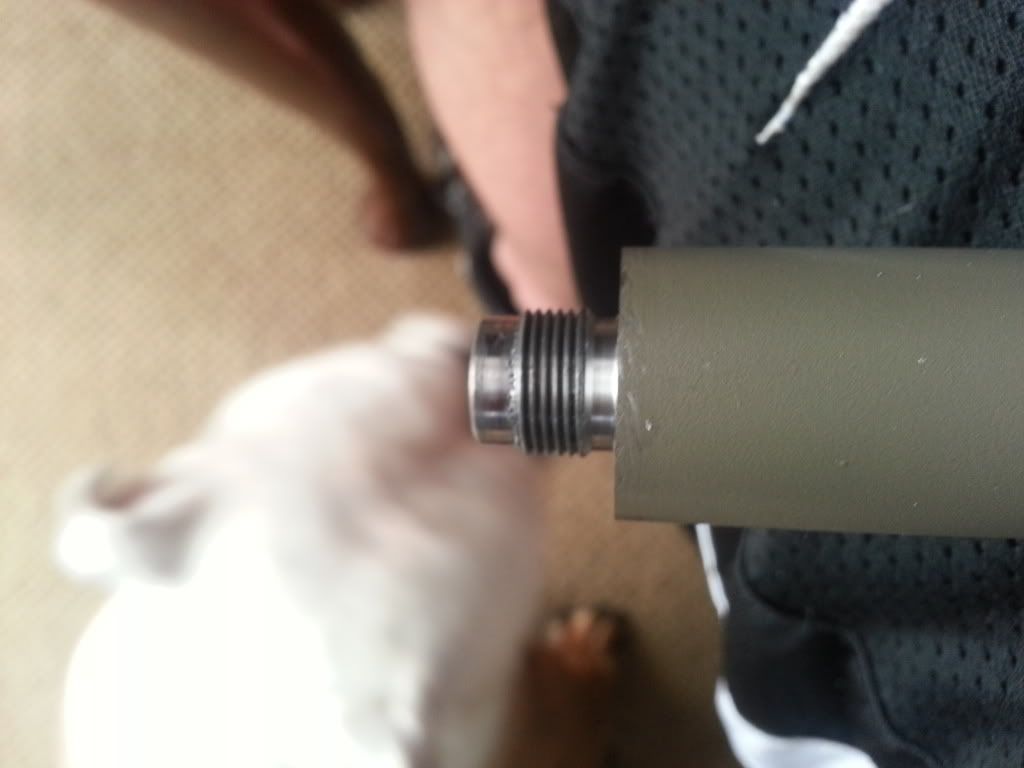
Last edited: