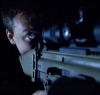
Shooting a match with the Kelbly’s Atlas Tactical wearing a Grayboe Ridgeback Stock and eating Lapua ammo
Introduction
When I first heard about Grayboe it sounded much like a division of McMillan. It was clear that Ryan, the Navy SEAL veteran son of CEO Kelly, was heading up the brand; but Kelly was also quoted in a lot of the press releases, the stocks were being made at the same location as McMillan stocks, and the Grayboe stock geometries were McMillan licensed. Last year at Shot 2017, I attended the McMillan press conference. At that event Kelly made statements to the effect that Grayboe was in no way affiliated with McMillan and really never was. He had helped his son get the ball started for a little while, but he was off and running now and no affiliation remained. At the same press conference, Kelly announced McMillan’s own lower priced line of stocks, the MC3 line. I thought: damn, these McMillans don’t mess around! I’ll help you get started today, son, but that doesn’t mean I’m not going after your market segment tomorrow. Of course, in the process of doing this review I asked Ryan about all this. He said the companies have always had separate ownership, but there was a time when Grayboe was located in the McMillan facility that he and Kelly were looking to find a path in which Grayboe and McMillan could coexist. That didn’t work out and it looked like the best option for both parties for Grayboe to locate to its own facility.
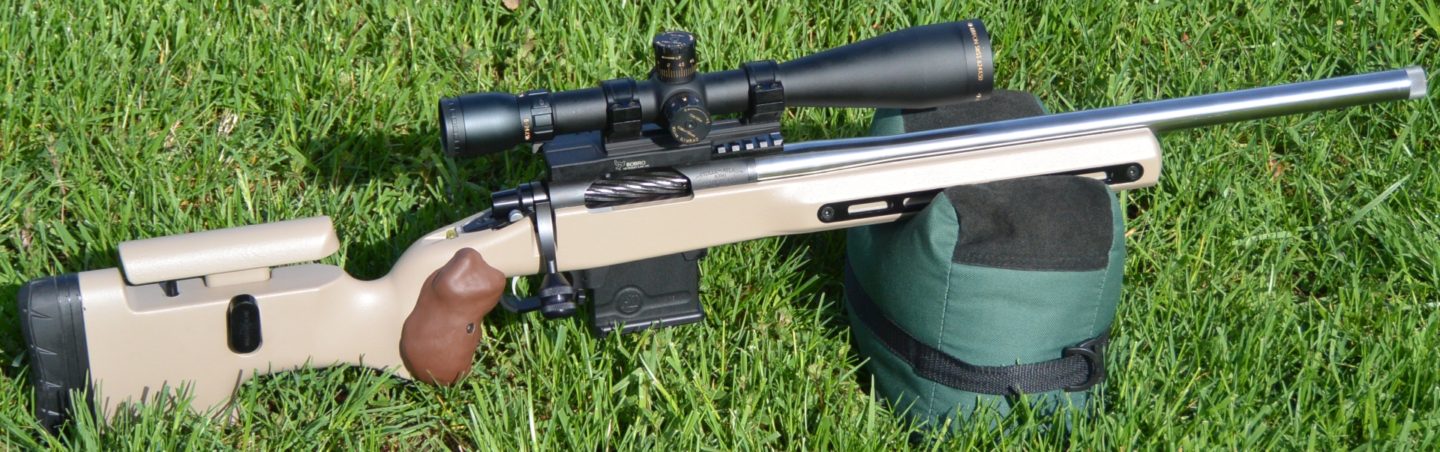
Table of Contents:
1) Grayboe stock technology
2) What a Grayboe stock is made of
3) Unboxing and initial impressions
4) Dimensions and measurements
5) Analysis
6) Upcoming plans
7) Conclusion
8) Pros and Cons
Grayboe stock technology
So, just what is a Grayboe stock? The shortest answer to that is that it is a composite stock. It is not, however, manufactured using the hand lay up method like most other composite stocks. This method involves impregnating fiber fabric with epoxy resin and laying it in a mold to form a shell which you later fill with a less dense fill material and, finally, machine to inlet. All this takes a minimum of 8 man hours per stock and is typically more like 12-14 hours total. The Grayboe material is epoxy based and includes fiberglass fibers and lightening agents similar to a traditional composite stock. The manufacture process, however, produces a non-directional uniform material. My initial suspicions were that this was through the use of an epoxy injection molding process similar to those used for things like transformer housings in the electronics industry. After grinding a bit on it during the bedding process, I suspect this is not the case, though, and that the molding process is lower pressure. Both small air voids (note the area machined deeper just below the front action screw) and places that appeared to have previously been voids but filled in (note the white fill just below or in front of the front action screw) were present.
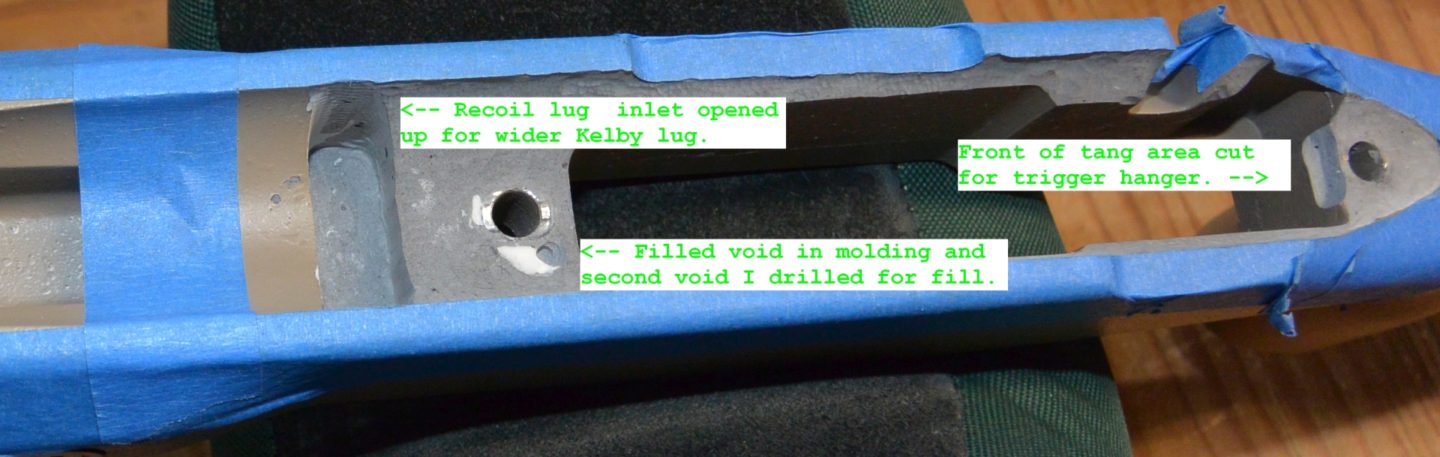
Grayboe developed its specific material formulations over several years and tests them at the composites center at USC. Their material provides excellent strength, stiffness, recoil absorption, and harmonics just as a traditional composite stock does. Because of its non-directional nature, you also get more flexibility in where you can machine it for add-ons. During this review I ground, machined, and drilled the material extensively. I can attest that it machines very easily and with remarkable smoothness. It cut so smoothly, in fact, that I didn’t need to sand the cut surface left at the ejection port. Grinding out room for bedding compound or drilling for attachments is done with ease and also without worry of compromising the shell structurally or creating a starting point for de-lamination. All of the machining I did for bedding and for adding my molded grip took less than two hours. I do recommend a respirator or dust mask when you do so, however: the grindings have a good bit of fiberglass in them and are very abrasive. Using Dremel high speed cutters at 15k rpms is optimal for a smooth even cut. I should also note that the paint used is very tough and did not chip out at the edge of any of my cuts or drills; this was very helpful in leaving a clean finish.
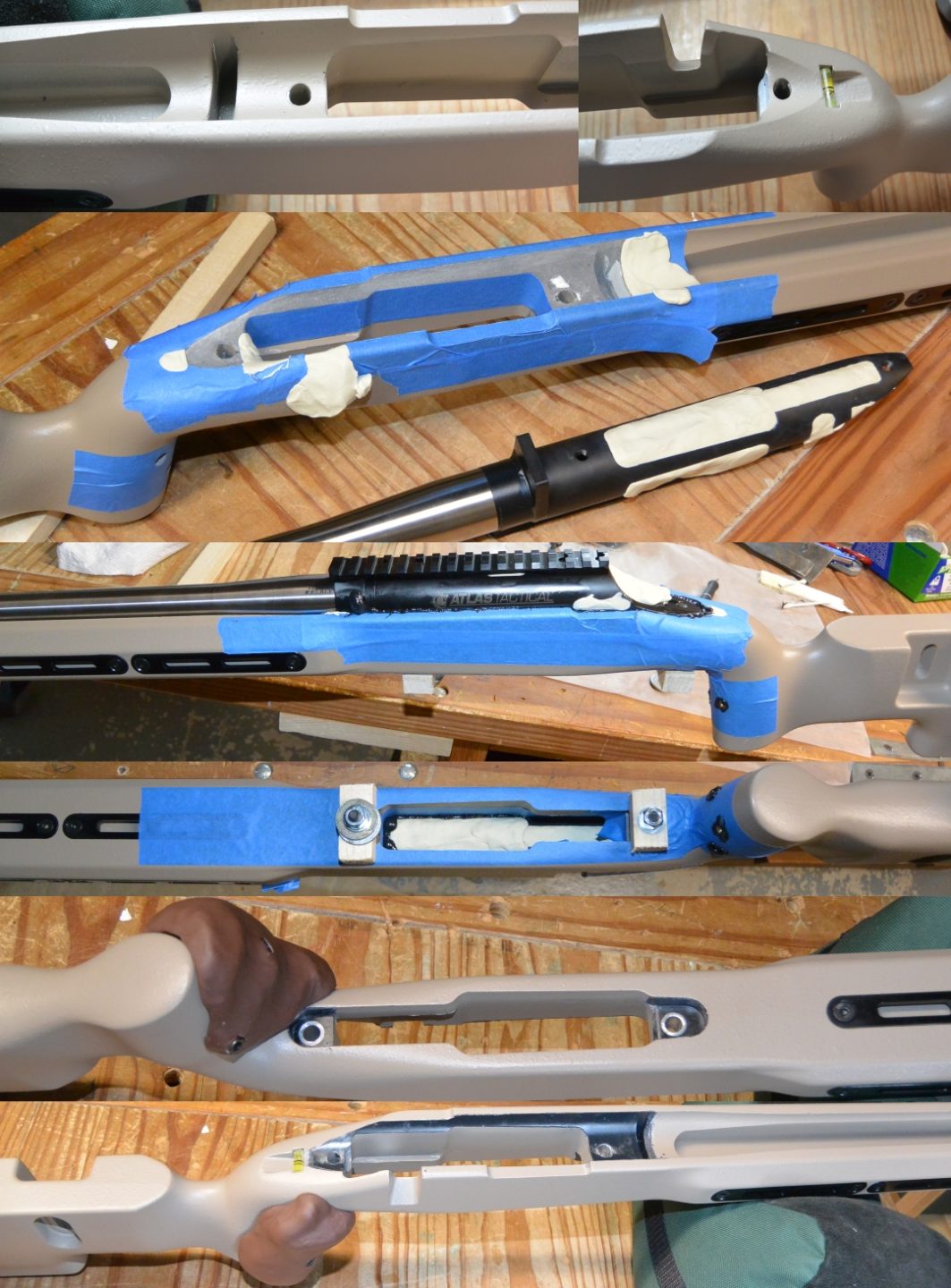
In my opinion, the biggest benefit of the Grayboe process is that, having eliminated the long labor hours of the hand lay up process, Grayboe stocks can be made at significantly less cost. The Ridgeback which I have here can be had with a quality DBM for $600 vs. around $1,000 that a comparable composite stock costs and, in addition, the Grayboe has a few more extras: such as a bubble level and M-Lok system. It is also important to note that although a Grayboe stock can be bedded even more easily than a traditionally made composite stock (depending on exactly how you have the traditional one prepped), though, you are more likely to skip this since the uniform material beneath the action is better suited to the unaided support of the action than the machined fill material in that section of a traditionally made composite stock. Furthermore, the Grayboe already has aluminum pillars molded in. It is my estimation that most custom rifle makers using Grayboe stocks will be bedding them but that most aftermarket buyers will not.
Unboxing and Impressions
The Grayboe arrived double boxed and well packed. Included with the stock were spacers for LOP and extra fasteners. The extra fasteners included two extra M-lock screws, a low profile option for the adjustable cheek piece, and longer screws for using the spacers on the pad to get longer LOP. Most notable in absentia is an M-lock flush cup. The stock has two rear flush cups molded in but no front ones. If you want to use a sling, you will have to add this via the M-lock system for about $20. The Ridgeback can be purchased without bottom metal for $500 from several sites or can be bought in a package deal with bottom metal for $600. I recommend the latter since you essentially get the MPA bottom metal for $100 in the package when it is usually $165. You should certainly buy the Grayboe from a third party site or through your rifle maker rather than direct because it is less expensive that way. You can use any other M5 inlet compatible bottom metal if the MPA isn’t the set of features you most like. I will also mention you can buy the Ridgeback in BDL configuration to use with the factory hinged floor plate bottom metal on a Remington 700.
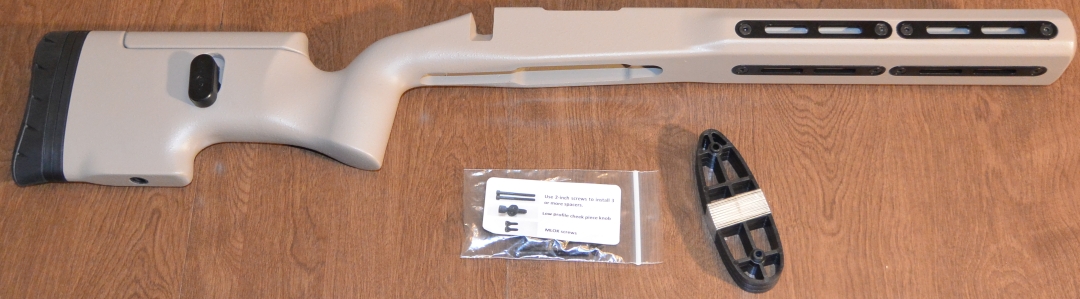
The first thing I noticed when looking over the stock was the less than clean paint inside the inletting. For some reason you are drawn to this and I have heard other owners also had this initial impression. You’re not going to see this area with the rifle in, and most stocks aren’t even painted here, but, for some reason, it is the first place you look. What you see is basically overspray from painting the outside of the stock a bit unevenly and clinging to a few loose fibers kicked up from the edge of the machining of some of the inletting. It is not a fair impression, but it is probably the one you will get first. I think much of this is because the rest of the stock looks clean and well fit so you are drawn to the one place you won’t end up seeing anyway: You have been warned.
The next thing I noticed was a little bit of aluminum under the paint in the DBM inlet. I hadn’t known that aluminum bedding pillars were molded in, so this was a big win. The pillars contribute to accuracy by making the stock essentially uncompressible under the action. It also makes it significantly easier for the end user to do a good quality bedding job. Seeing this second was interesting: my first impression had been that maybe this wasn’t as good a stock as I thought it was going to be and then it was immediately followed by the thought that maybe it was better.
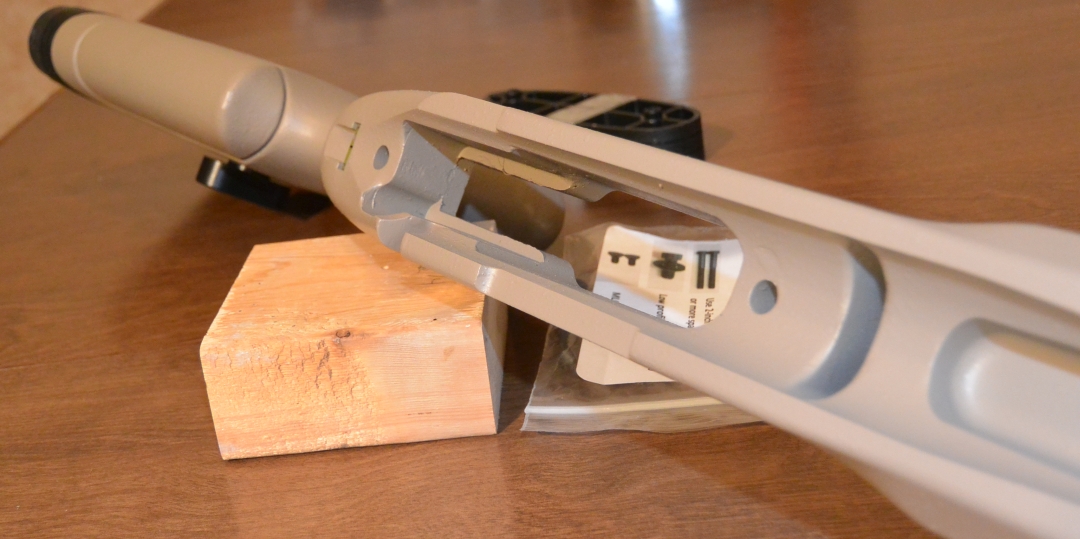
That thought continued as I went down the stock area by area. The recoil pad (a Browning Inflex) felt very good; better than I expected on a moderately priced stock. The 6 M-lock inserts (2 left, 2 right, and 2 bottom) are very nicely fitted and the stock fore end has been specifically designed to accommodate the relief underneath the inserts. The adjustable cheek piece is Grayboe’s own design: much easier to manufacture and a big departure from the norm. I had been wary when I saw some pictures of the prototypes as they had no guide rods and I did not see how you could keep it from rocking. In the production version they have added a single guide rod to the design and it is rock solid. It left me wondering why nobody had tried it before. The more I thought about it, the more I realized that our designs in the way of cheek pieces basically come down to what is easy to do in wood. The Grayboe’s new design would not work in wood but is pretty easy to do with any molded material. I am actually a little surprised that something like this was not developed earlier given how much easier, and less time consuming, it is to do in any molded stock than a traditional cheek piece. In fact, many molded stocks actually use the exact cheek piece hardware that was originally designed to be put in a wood stock and is still used on wood stocks. Putting this hardware in a hand lay up composite stock, for instance, is not the easiest thing to do since the shell and fill body of the composite stock is very different than the structure of wood. All that being said, although the Grayboe system is as good as most traditional cheek systems, it does not have the quick removal or lateral adjust of the better systems such as the Warner.
Dimensions and Measurements
Grayboe’s website is pretty sparse to start with and compounds that
with being a bit nebulous, so I was not sure of really any of the specs
when I received the stock. Here is what I have measured:
– Weight: 58.3oz (3.64lbs) This is basically exactly what a McMillan A5 adjustable fiberglass stock averages
– Recoil lug slot thickness: 0.3565″
– Recoil lug slot depth: 0.5455″
– Recoil lug slot width: 1.34″
* Note: The back of the recoil slot is a little rounded at the
edges. If your custom action has a full width recoil lug, it will not
totally center on the action holes without inletting the recoil lug slot
edges some.
– Barrel channel width at stock front end: 1.034″
* Note: The fit on a Sendero contour barrel is perfect.
– Width of fore end: 2.524″
– Inlet: M5, Grayboe sells a Mesa Precision arms one but you can use any. DBM is not included with stock.
– It has a bubble level in the stock
– LOP range (with included parts and stock rem trigger) 12.5″ –
13.885″ with 5x .277″ spacers. Presumably, you could get more spacers
and longer machine screws.
– Paint is Polane T 2 part polyurethane. The stock can be painted with Cerakote and baked at 400 for 20min without a problem.
Analysis
I have found the strength, stiffness, and feel of the Grayboe to be
excellent. The spacing of the pillars and their depth was also perfect,
as was the bottom metal fit. Fit on my Kelbly action was not drop-in and
it will not be so on many custom actions. Custom actions have some
variance in many dimensions. In the case of my Kelbly, it uses a trigger
hanger, a wider trapezoidal recoil lug, and a longer ejection port.
Accommodating each of these required some removal of stock material.
The stock is both usable unbedded and very easy to bed as a result of the easily workable material and the already present and properly placed aluminum pillars. The M-lok slots on three sides of the fore end coupled with the strength and stiffness of the material will be of excellent use to a PRS shooter in attaching barricade stops. The Grayboe should be quite competitive with chassis in this respect and have a good leg up on traditional composite stocks. The level, though it looks cheap, is functional, can be seen in shooting position, and is actually level.
The grip area, like any A5 style stock, provides a terrible hand position to the shooter with very poor hand contact with the stock when proper trigger finger position is employed unless you have the hands of Shaq. As shown in the pictures, I added #10×32 threaded brass injection molding inserts to the stock while I was bedding it. I use these inserts to fasten a molded polymer clay grip to the stock. These can be made for about $10 from oven hardening polymer clay available at any craft store: I highly recommend this. Building up and custom fitting the grip area of a stock is done in most of the older shooting sports that involve support of the rifle by the shooter. Biathlon and 3-position are excellent examples of this. It should be expected that PRS competitors will see the same benefits.
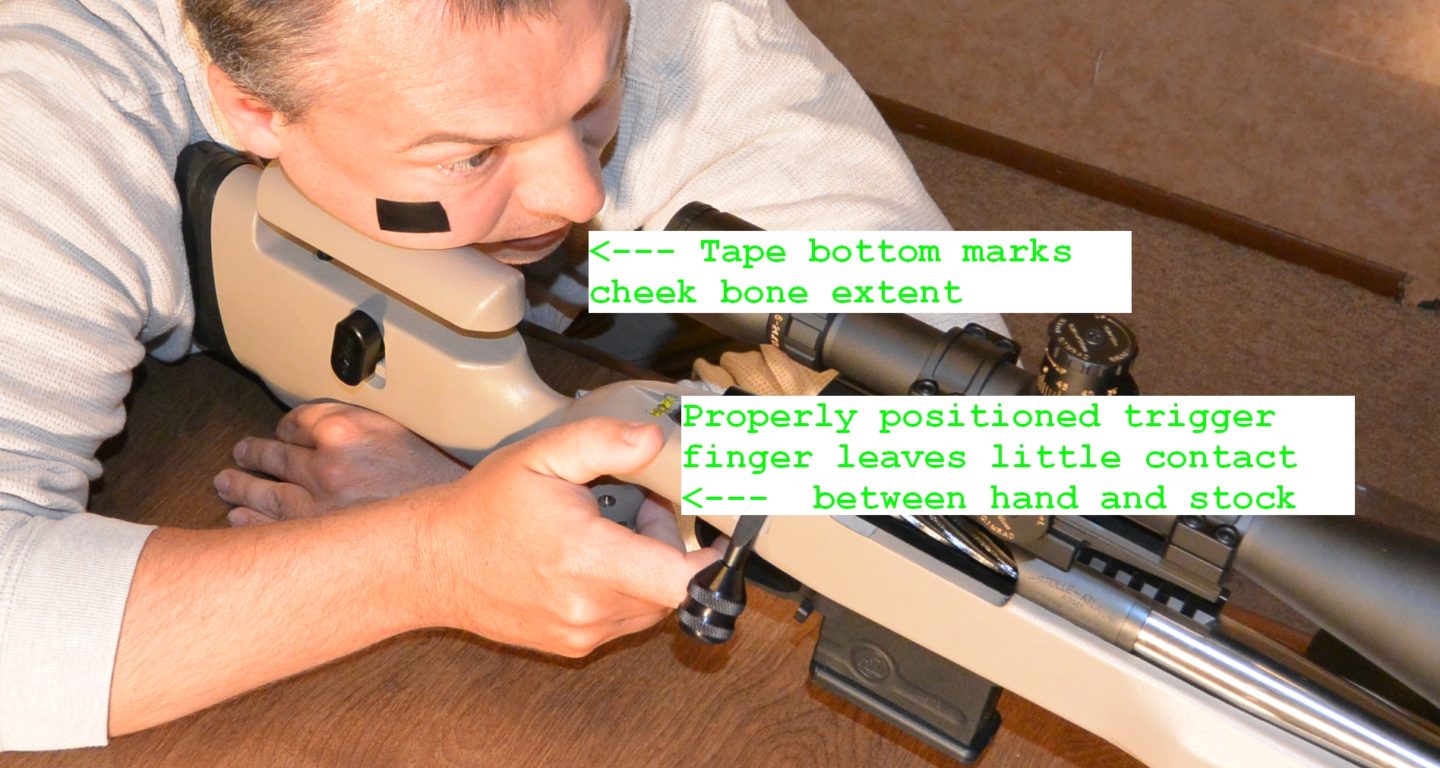
With my facial dimensions, adjustable cheek pieces are a must if I want a good weld. I don’t even look at stocks that don’t have one. Just as with the grip, I find that proper fit on the cheek piece is essential. These are contact points where your body and the rifle meet. Proper fit means better control of the rifle and, consequently, more accuracy. This is greatly amplified by positions requiring the shooter (as opposed to inanimate objects) to support the rifle. The adjustable piece on the Ridgeback unfortunately has a rather small range of adjustment at only 3/4″ and, more importantly, starts rather low (below the bolt). This compares with more than 1″ of adjustment range on the Warner Tool one on my 3-position gun. The height might be just enough, with a small objective scope on ultra-low mounts, to get me to center line, but is at least 1/2″ shy of correct with my current arrangement. Hopefully, Grayboe will simply offer a higher comb piece to slip in later so that those in my condition can simply buy one that starts 3/4″ higher. Failing that, I will have to add a polymer clay riser to the cheek piece as fit is of paramount importance to performance. It should also be noted that in order to clean the rifle, the Grayboe cheek piece must be fully lowered or removed. It does not have a snap-off feature as some premium aftermarket units like the Warner do. It also doesn’t have lateral adjustment, though I have never really found that to be of great importance and don’t use it on my 3-position rifle even though I have it.
Upcoming plans
Grayboe currently offers just four stock models, with only the Ridgeback being adjustable out of the box. They are, of course, planning to expand this. Additionally, they are continuing to fine tune the molding process and other aspects of the manufacture. I mentioned earlier that the inletting for my bedding revealed some voids. These are time consuming to fill and not ideal to have. There is therefore room for improvement in the process both in terms of price and quality. Grayboe is also working on weight reduction by tinkering with the fibers and matrix so at some point I expect we will see carbon models.
Conclusion
The pricing on Grayboe stocks is closer to that of a polymer stock
than a traditional composite. Without question, though, its performance
and characteristics are much closer those of a traditional composite
stock. In a few respects, such as the M-lok fore end and drop in
performance, I think it is superior to a traditional composite. In a few
other ways, including the alterations necessary to fit custom parts;
the appearance; the number of models available; and the weight, I think
it gives up ground to traditional hand laid composites. The very
comparison though is quite telling. At $600 with DBM bottom metal, these
stocks are an excellent value. I am quite satisfied to have my
excellent new Kelbly rifle wearing one.
Pros and Cons
Pros:
– It is very affordable at $600 with DBM bottom metal
– Harmonics, recoil absorption, and temperature and moisture stability characteristics are similar to traditional composites
– Stiff and strong
– Aluminum pillars are molded in and perfectly spaced
– Inletting dimensions in general are correct
– Very nicely machinable for bedding and other add-ons
– Feature rich with a bubble level, M-lok fore end, and adjustable LOP and comb
– Durable paint used with a variety of colors available
– Recoil pad included is a good one
– Well designed for good performance, bedded or unbedded
Cons:
– The adjustable comb has limited range and does not go high enough for many users
– The grip area will not provide good hand position for probably 90% of users
– You get the M-lok but no attachments so you will be out $50 for sling and bipod attachment points
– Stock is inherently not a custom piece and will require alteration for many actions
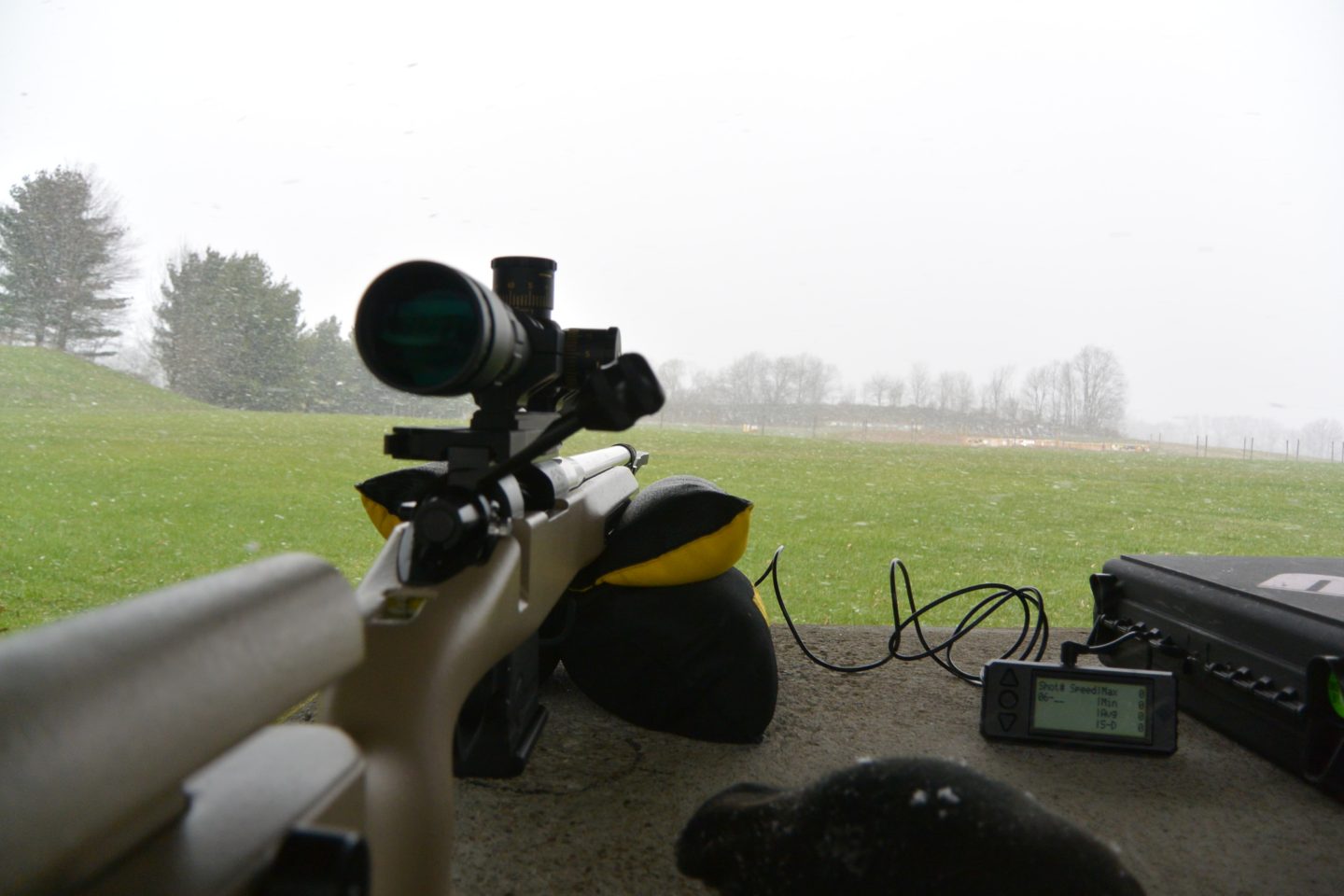