Ok So im finally starting my rifle project. Im $1900 invested up to this point, so i don't want to ruin the stock. My issue is i want to install this
150-108 Stock Embedding Spigot Versa-Pod Bipod Adapter
So has anyone here modified a HS Precision stock? I'll need to drill a hole about 8" deep into the forearm, and then decide what to use to epoxy/glue the spigot into place. I know there is other ways of attaching my Fortmeier bipod but this is how i want my end results to look, feel, and function.
Below is a photo of my rifle (Savage 110 FCP HS Precision in 300 PRC, SKU Number. 22088) using the dual swivel stud mounting holes with a picatinny rail i had, that just happened to fit perfectly, and the rail to spigot adaptor that came with the bipod
And this is how i want my finished bipod set up to look, feel, and function. This is just sitting in place for a mockup to give a better understanding.
150-108 Stock Embedding Spigot Versa-Pod Bipod Adapter
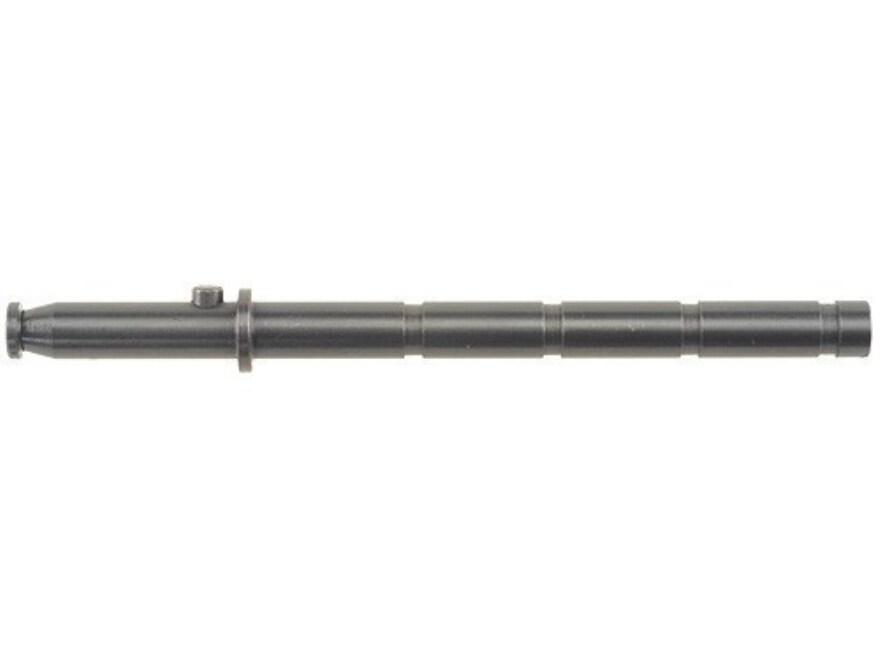
So has anyone here modified a HS Precision stock? I'll need to drill a hole about 8" deep into the forearm, and then decide what to use to epoxy/glue the spigot into place. I know there is other ways of attaching my Fortmeier bipod but this is how i want my end results to look, feel, and function.
Below is a photo of my rifle (Savage 110 FCP HS Precision in 300 PRC, SKU Number. 22088) using the dual swivel stud mounting holes with a picatinny rail i had, that just happened to fit perfectly, and the rail to spigot adaptor that came with the bipod

And this is how i want my finished bipod set up to look, feel, and function. This is just sitting in place for a mockup to give a better understanding.
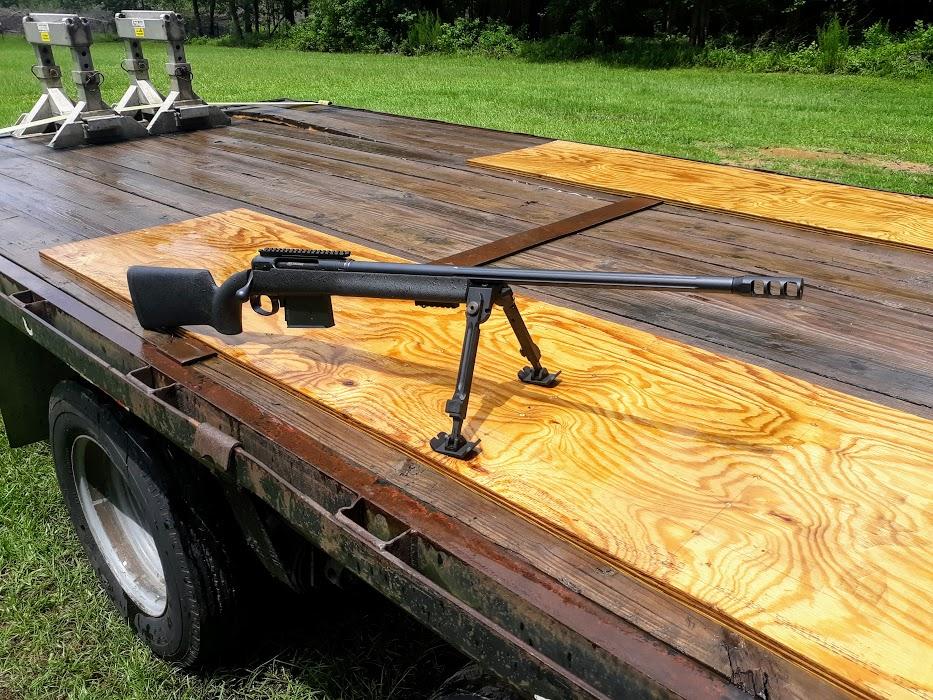
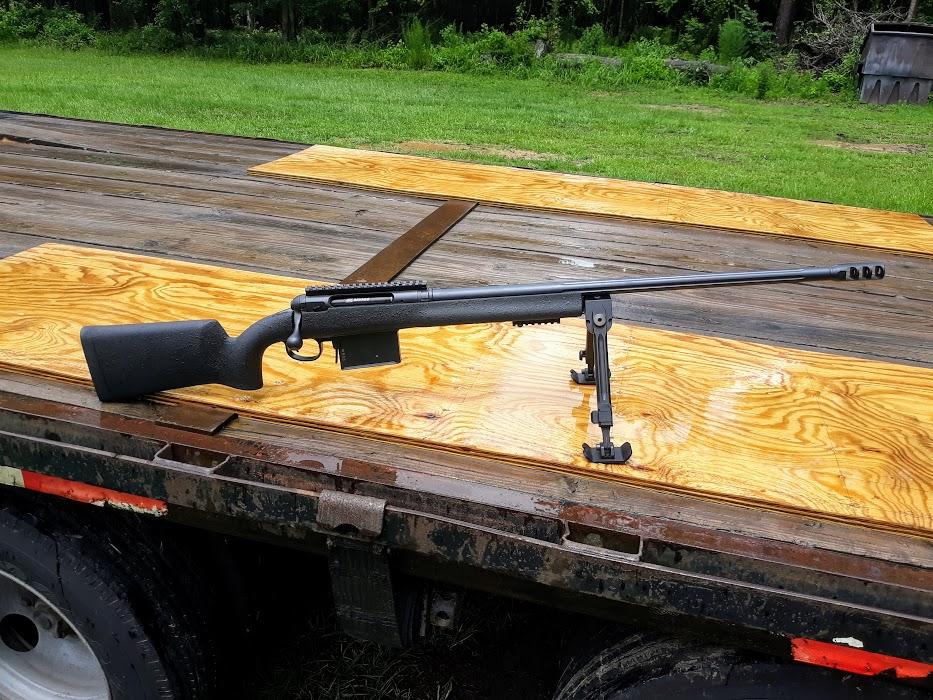
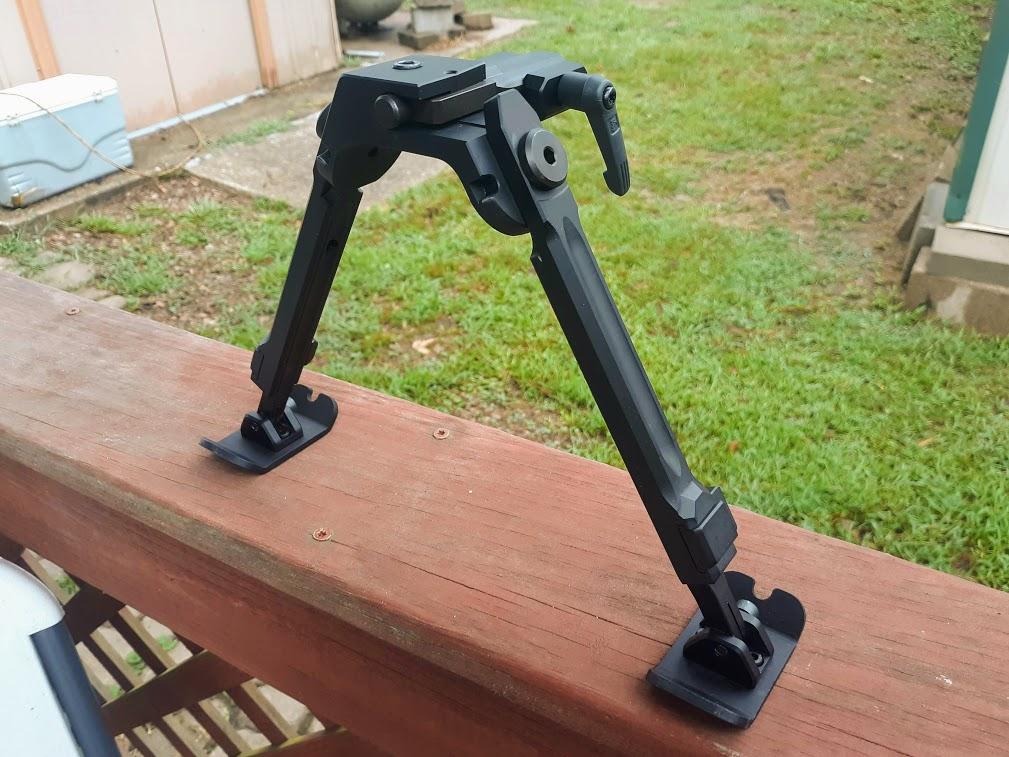