you guys know the basics, I cut the factory knob into a 5/16 square with a die grinder and cutoff wheel, shaped it round with a bench grinder (ended up right at .300, .311 gave me hell getting the die going).
I'll take a moment to say if you're doing this and don't have real cutting fluid GET SOME before you start. I couldn't find mine (hadn't used it since moving a year ago) so tried to cheat with 3-in-1 oil, that was NOT happening. I like RotaMagic from the local welding supply shop, rapidtap works great too.
Now, the Surgeon knobs as you probably know are much longer than the typical rem knobs and smaller in diameter. I could run the threads all the way up to where the handle bends I think and still not have issues hitting my finger, so I could have just chopped off the factory knob completely and threaded the handle itself BUT the handle is not thick enough to cut 5/16 threads. I chose to go the "normal" route so I'd have a threaded guide to run threads further up the handle if needed. Plus I can always make it a bit shorter, hard to make it longer. I cut just shy of 1" of threads onto the handle (Surgeon knob has 1.1" of threads, I ran the die to .925ish)
Once I decide on my finished length I'll blend the joint to purdy it up. I'm happy with the straightness of it, I have seen a few garage jobs that are grossly crooked and would not be happy with that, no offense there it just would bug me.
Enjoy!
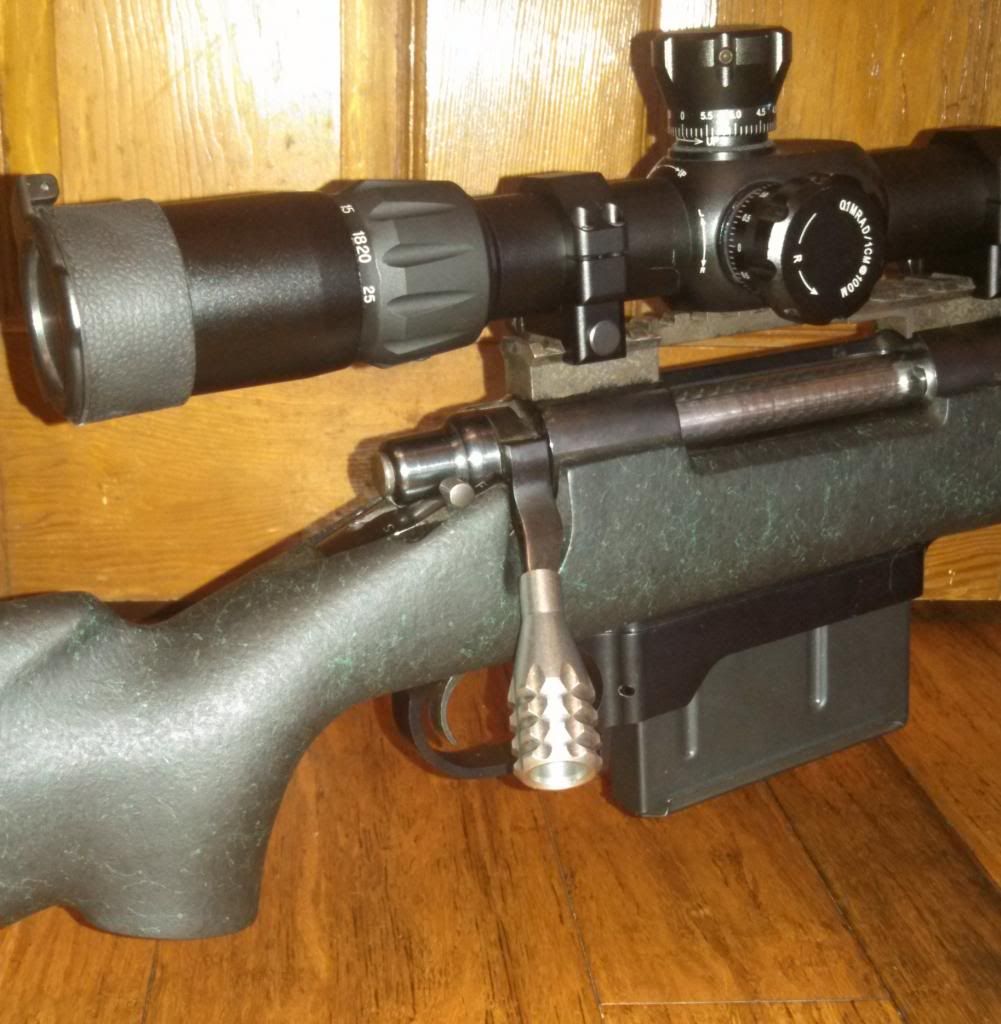
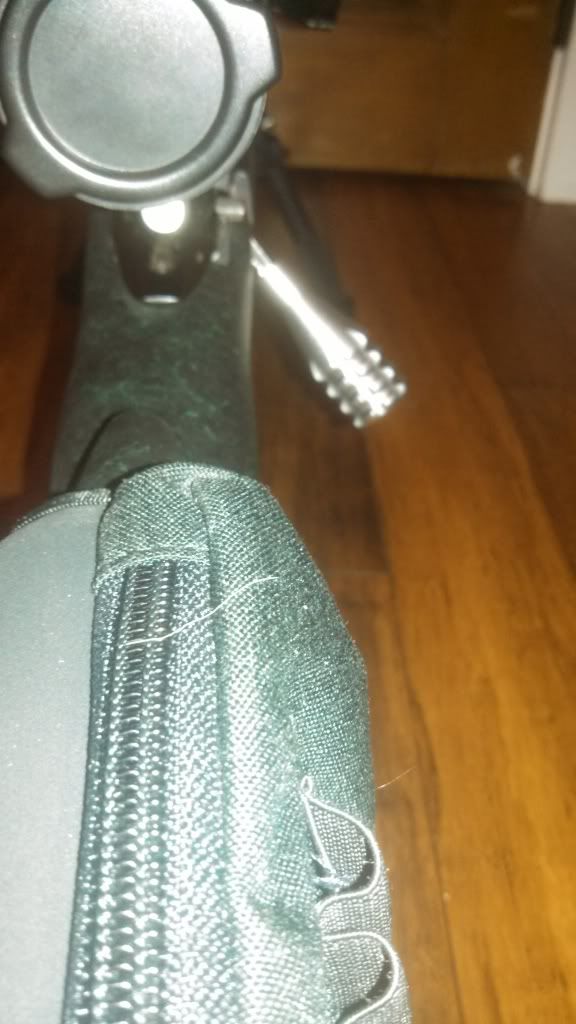
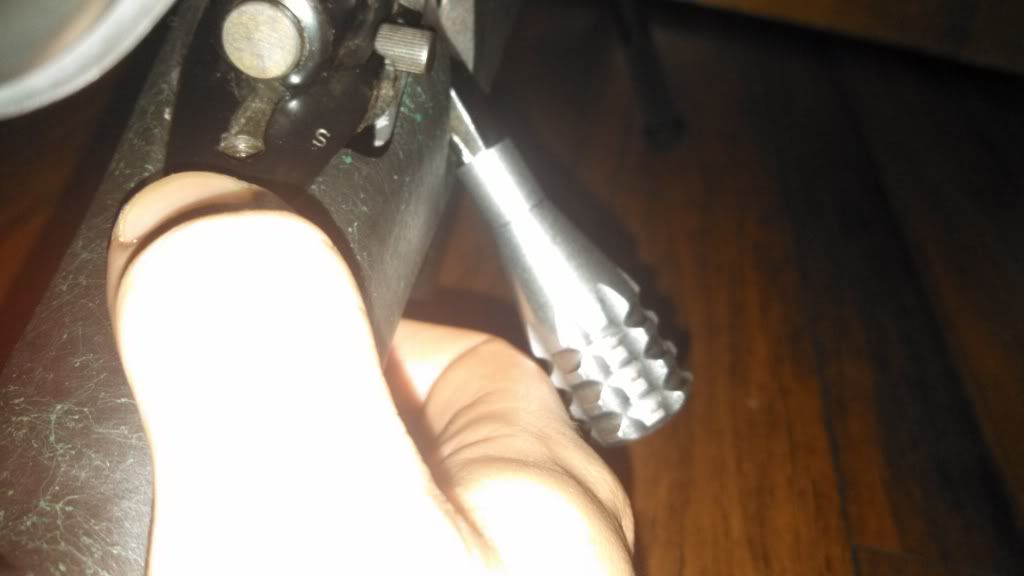
I'll take a moment to say if you're doing this and don't have real cutting fluid GET SOME before you start. I couldn't find mine (hadn't used it since moving a year ago) so tried to cheat with 3-in-1 oil, that was NOT happening. I like RotaMagic from the local welding supply shop, rapidtap works great too.
Now, the Surgeon knobs as you probably know are much longer than the typical rem knobs and smaller in diameter. I could run the threads all the way up to where the handle bends I think and still not have issues hitting my finger, so I could have just chopped off the factory knob completely and threaded the handle itself BUT the handle is not thick enough to cut 5/16 threads. I chose to go the "normal" route so I'd have a threaded guide to run threads further up the handle if needed. Plus I can always make it a bit shorter, hard to make it longer. I cut just shy of 1" of threads onto the handle (Surgeon knob has 1.1" of threads, I ran the die to .925ish)
Once I decide on my finished length I'll blend the joint to purdy it up. I'm happy with the straightness of it, I have seen a few garage jobs that are grossly crooked and would not be happy with that, no offense there it just would bug me.
Enjoy!
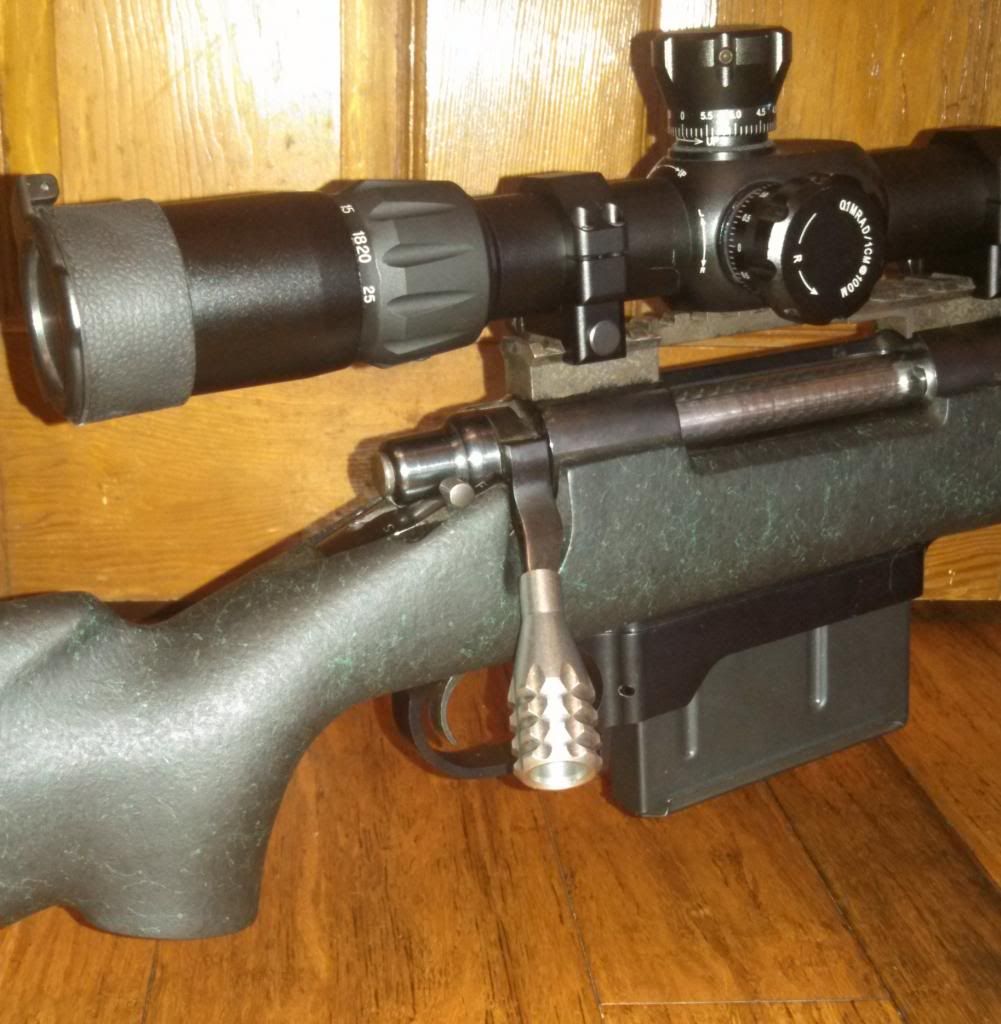
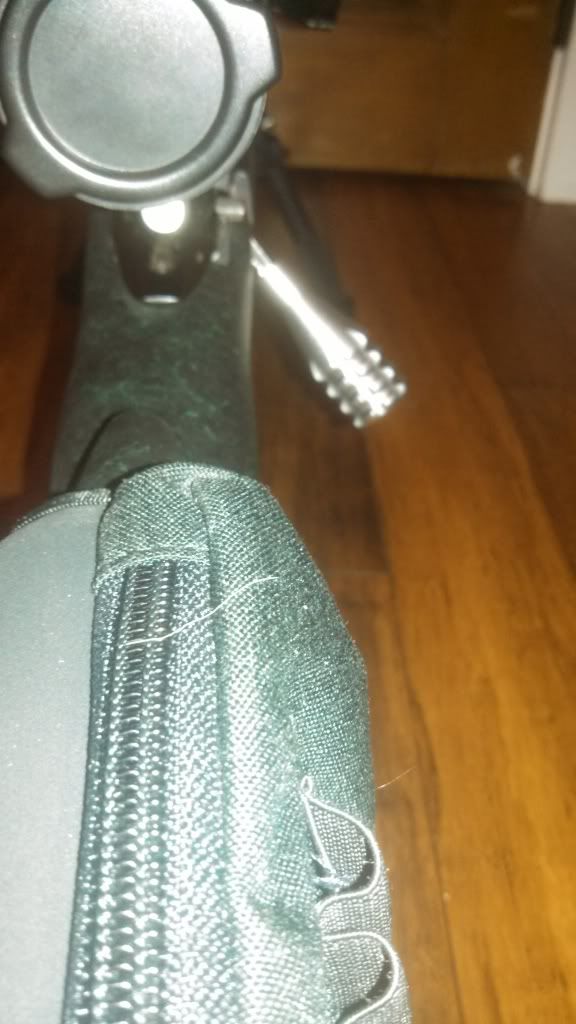
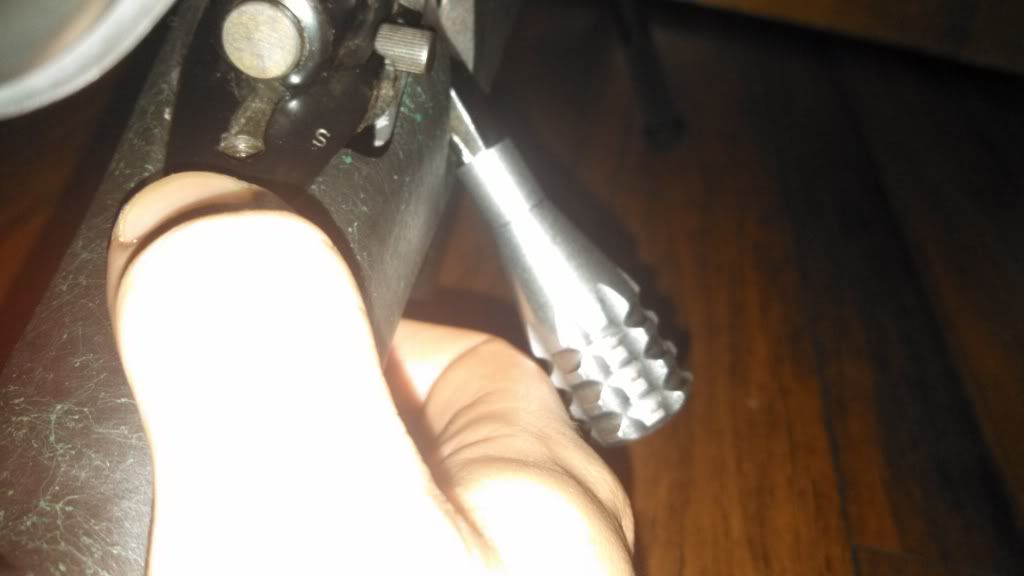
Last edited: