Update! Finally got some more brass to play around with.
I ended up with some virgin Norma .300 and 7mm RSAUM brass.
Specs on the brass were:
7mm
COAL: .225-.227
Inside Neck Diameter: .290
Outside Neck Diameter: .312
Neck Thickness: .016-.017
300
COAL: .210-.212
Inside Neck Diameter: .304
Outside Neck Diameter: .336
Neck Thickness: .015-.016
The Neck Thickness in the brass varied from piece to piece, but a pretty constant average would be around .016
To work the .300 brass:
- Ran it through a Whidden Full Length 6.5 SAUM Bushing Die
- Used a .331 / .317 / .303 / .291 Bushing
After that process I ended up with a .257 Inside Neck Diameter, which is obviously smaller than what you need. Per the original post a .295 Bushing would probably be optimal for this. I used the .291 because I already had it, and didn't figure the .004 difference would make a big deal. I then ran it through a Sinclair 6.5 expander, which took the Inside Neck Diameter up to .261-.262. Based on those numbers, the Neck Thickness increased by .001-.002 to .017-.018
With that much brass getting pushed around, as per my earlier work, I was pretty sure that there was going to be a "Donut" (thicker area) somewhere. I used some Pin Gages to check the inside neck for any variation in thickness. I ran a .261 and it made it through all of the necks with no problem. I then ran a .262 through, and it would make it about 3/4s of the way down the neck before stopping. That puts a thicker area of brass on the inside of the neck just above the shoulder junction.
Per my earlier post, I am taking care of that by neck turning both the inside and outside, and adjusted it so that it gives me a finished uniform neck thickness of .015. I am then finishing that with the .291 bushing which gives me a final Internal Neck Diameter of .261, that takes care of the .300 brass.
To work the 7mm brass:
- Ran it through a Whidden Full Length 6.5 SAUM Bushing Die
- Used a .303 / .291 Bushing
As I was checking it out, I realized that about the last .030-.050 of the neck closest to the shoulder was not getting sized!
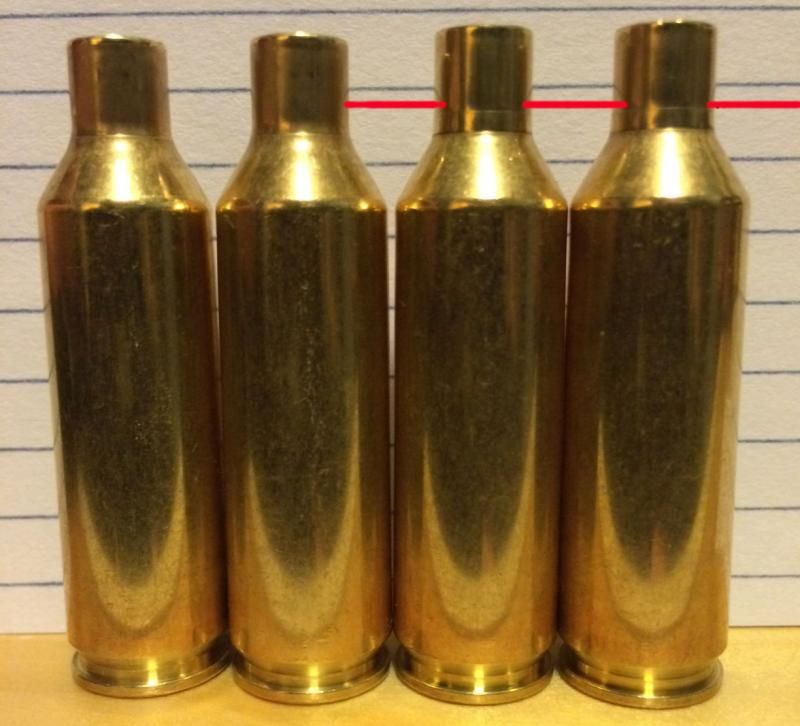
Long story short, I tried everything that I could to get that part of the neck sized, but the only thing that worked was to take about .030 off of the top of the shell holder and then reset the die lower in the press. That did finally get it right to the neck/shoulder junction.
As per above, after that process I ended up with a .257 Inside Neck Diameter.
I then ran it through a Sinclair 6.5 expander, which took the Inside Neck Diameter up to .261-.262. Based on those numbers, the Neck Thickness increased very slightly, but not as much as with the .300, it was no more than .001.
I then checked the inside neck dimensions with the Pin Gages to double check for a Donut, the .261 made it through with no problem, and the .262 also made it through, in some cases it was pretty snug, but it never made a hard stop like with the .300 brass.
I am also going to finish this with the inside & outside neck turning to produce a .015 Neck Thickness, and then run it through the .291 bushing, for consistency purposes to produce a finished Inside Neck Diameter of .261
ADDITONAL NOTES!
- the necks on the brass were really bad out of the box (concentricity and thickness). I would seriously recommend cleaning them up with passes through FL dies with expanders, then checking them with every tool that you have, prior to doing any neck turning. Simply using a bushing die, without the expander, my brass was all over the place when I checked it with a Sinclair Neck Gauge.
- the necks on the virgin 7mm & 300 brass are not the same. The 7mm is longer, so make sure you account for that as needed (issue below)
- make sure your necks are sized completely, per above, I had about a .030-.050 area just above the shoulder junction that was not getting sized down. If you didn't catch this and correct it before you started turning, that area would have more material removed making it thinner and inconsistent.
Hopefully this may clarify some things, if not please let me know.